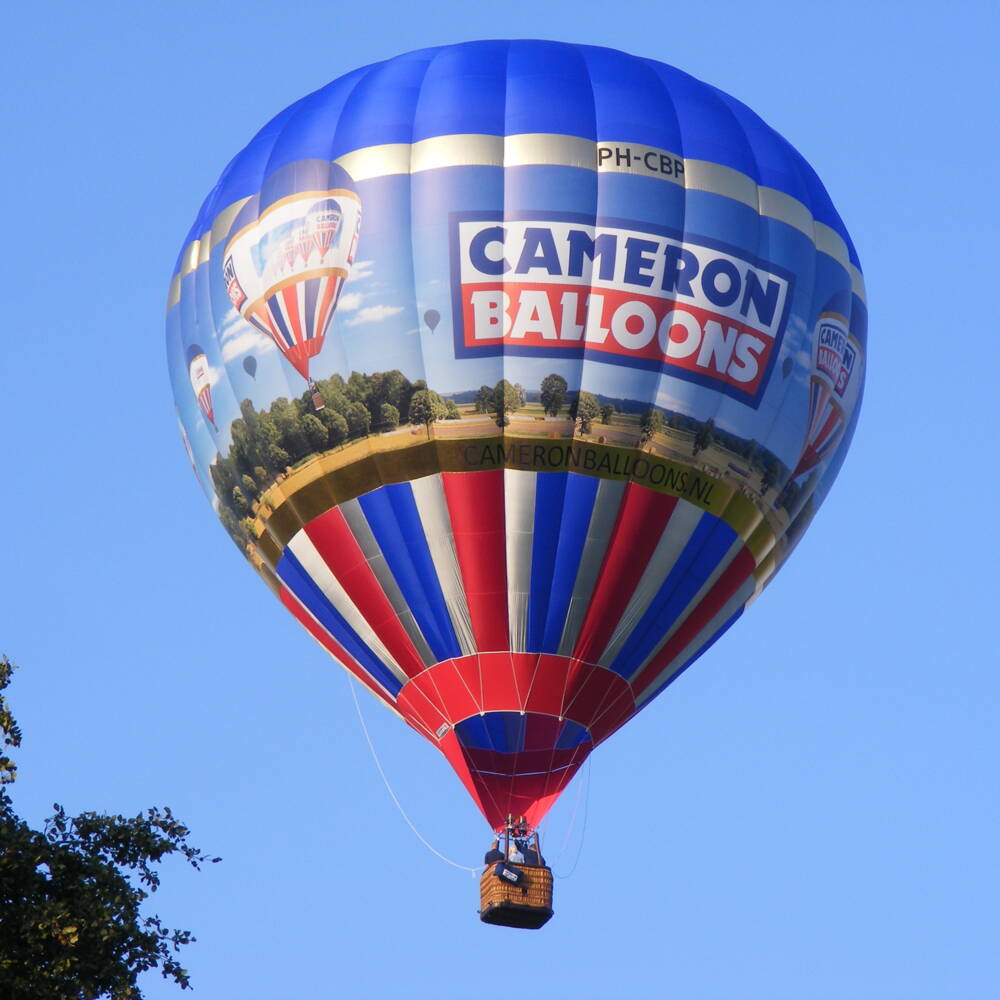
Cameron Balloons digitalisiert und automatisiert den Textilzuschnitt
Cameron Balloons hat mit der Investition in einen Zünd Cutter G3 L-2500 seinen Herstellungsprozess revolutioniert.
Das in Bristol (Großbritannien) ansässige Unternehmen, das 1971 von Don Cameron gegründet wurde, stellt Heissluftballons her. In den Anfängen der Unternehmensgeschichte startete Cameron die Produktion der Heissluftballons im Keller seines Hauses. 1983 zog Cameron Balloons an seinen aktuellen Standort. Der Betrieb erstreckt sich über drei Etagen. Der grösste Teil der Betriebsfläche wird genutzt, um riesige Bahnen bunter Stoffe auszulegen, die dann zugeschnitten und von Fachpersonal zusammengenäht werden. 1989 erhielt das Unternehmen mit dem „Queen's Award for Export“ königliche Anerkennung. Im Jahr 2000 wurde es mit dem „Prince Philip’s Designers Prize“ für herausragende Designleistungen für Business und Gesellschaft ausgezeichnet.
Das Unternehmen stellt Heissluftballons in allen Materialien, Grössen, Formen und Arten her. Die meisten Ballons mit Sonderform werden für kommerzielle Werbung produziert, aber einige werden auch von Privaten erworben, zum Beispiel vom inzwischen verstorbenen Verleger Malcolm Forbes. Seine Bestellung umfasste rund ein Dutzend Ballons in Sonderformen wie Harley-Davidson-Motorrad, Sphinx, Beethoven-Büste, französisches Chateau, Pagode und Minarett. Das Unternehmen produziert auch Luftschiffe oder Helium-Ballons. Es war bereits an nationalen und internationalen Weltrekorden im Bereich Ballonflug beteiligt, darunter die schnellste Weltumrundung, sowie der höchste und der weiteste Flug der Welt.
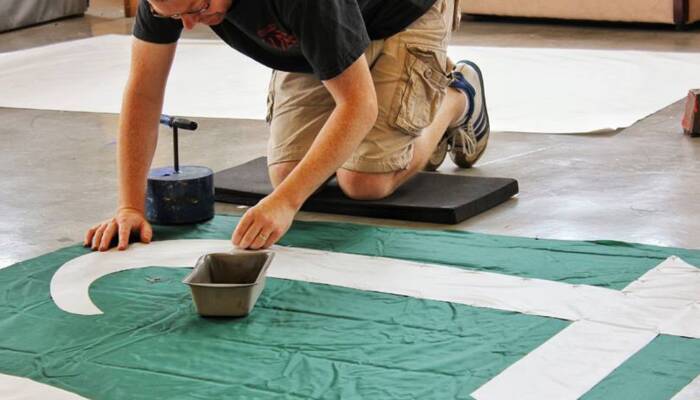
Nick Purvis, Sales Director bei Cameron Balloons erklärt: „Jeder unserer Heissluftballons wird nach den strengen Standards der britischen Civil Aviation Authority gefertigt, und wir müssen uns an dieselben strikten Verfahrensweisen wie jedes andere Luftfahrtunternehmen halten.“ Cameron Balloons ist mit mehr als 9.500 international ausgelieferten Heissluftballons einer der weltweit führenden Anbieter auf dem Markt. Nick Purvis berichtet: „Das Unternehmen ist enorm gewachsen. Wir haben mit wenigen Mitarbeitern begonnen, die den Ballonstoff damals noch mit der Hand schnitten und zusammennähten. Heute beschäftigen wir rund 50 Mitarbeiter, die innovative Maschinen für die Produktion bedienen. Wir haben im Laufe der Jahre verstärkt in Technologie investiert, um unsere Herstellungsprozesse effizient zu machen.“
Die Heissluftballons werden aus einem sehr fein gewebten Nylon gefertigt, das 35 bis 100g/m2 wiegt. Das leichte Material wird in der Regel in symmetrische Teile in Form von Booten geschnitten. Die vielen Kilometer Stoff, die zur Herstellung eines Ballons erforderlich sind, werden dann vom Fachpersonal zusammengenäht. Nick Purvis erklärt: „Jeder Heissluftballon wird genau nach den Anforderungen unserer Kunden hergestellt, wobei die durchschnittliche Durchlaufzeit 10 bis 30 Wochen beträgt, je nachdem, wie komplex die grafischen Elemente und die Form des Ballons sind.“
Cameron Balloons setzt seit mehr als 20 Jahren auf digitale Schneidtechnologie von Zünd, um die unterschiedlichen Stoffe für die einzelnen Panels zuzuschneiden. Nick Purvis fügt hinzu: „Den Grossteil der Schneide-Arbeit machen wir mit dem Driven Rotary Tool DRT von Zünd. Der Zünd Cutter ist zudem perfekt für den Zuschnitt von Grafikelementen oder Buchstaben für das Branding des Heissluftballons.“ Auf dem vielseitigen Zünd Cutter setzt Cameron Balloons auch das Markiermodul MAM ein, um die einzelnen Panels zu beschriften.
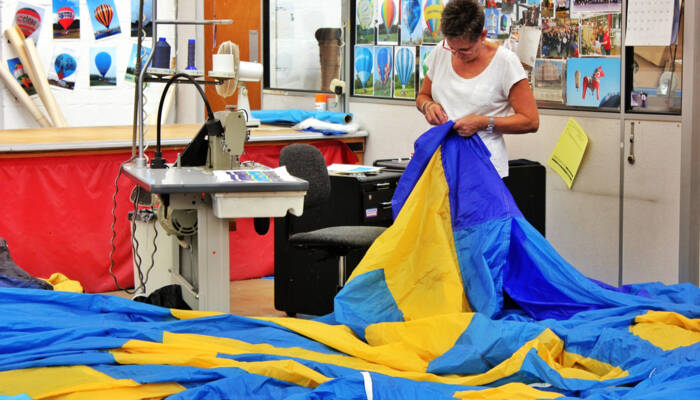
Das Unternehmen investiert zum mittlerweile dritten Mal in digitale Schneidtechnologie von Zünd. Den ersten Zünd Cutter hat der Betrieb in den frühen Neunzigerjahren erworben, um Muster zu plotten und Stoff-Panels zuzuschneiden. Nick Purvis: „Unsere neueste Errungenschaft ist der Zünd Cutter G3 L-2500. Dieser Cutter hat unseren Herstellungsprozess revolutioniert. Bei der Auswahl des Zubehörs haben wir uns für die Integrated Compact Colour-Kamera (ICC) entschieden, um den Prozess mit unserem Durst-Drucker zu automatisieren. Die Vorteile, die daraus resultieren, haben unsere Erwartungen übertroffen. Früher mussten wir das Material nach dem Bedrucken mit dem Durst-Drucker manuell zuschneiden, bevor es an den Zünd-Cutter übergeben werden konnte. Dank der ICC-Kamera kann der Cutter jetzt Registriermarken und Materialkanten erkennen und das Material präzise zuschneiden. Die Zünd-Technologie und der Durst-Drucker arbeiten perfekt zusammen.“ Das bedruckte Material wird jetzt direkt an den Cutter übergeben. Nick stellt abschliessend fest: „Seitdem wir den Zünd G3 Cutter durch die ICC-Kamera ergänzt haben, konnten wir ein Höchstmass an Effizienz und Präzision erreichen. Wir sparen jetzt jedes Jahr rund 4% Material.“
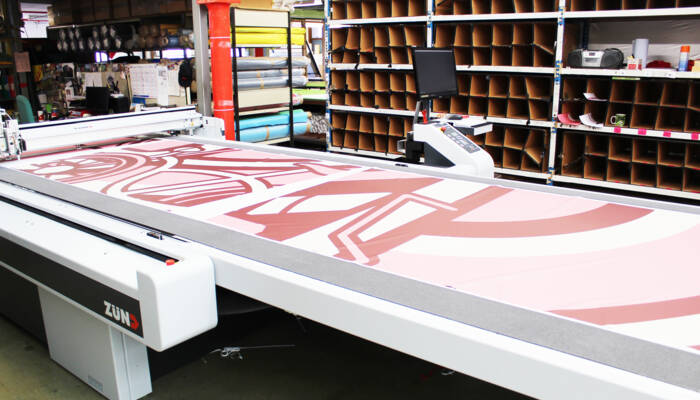