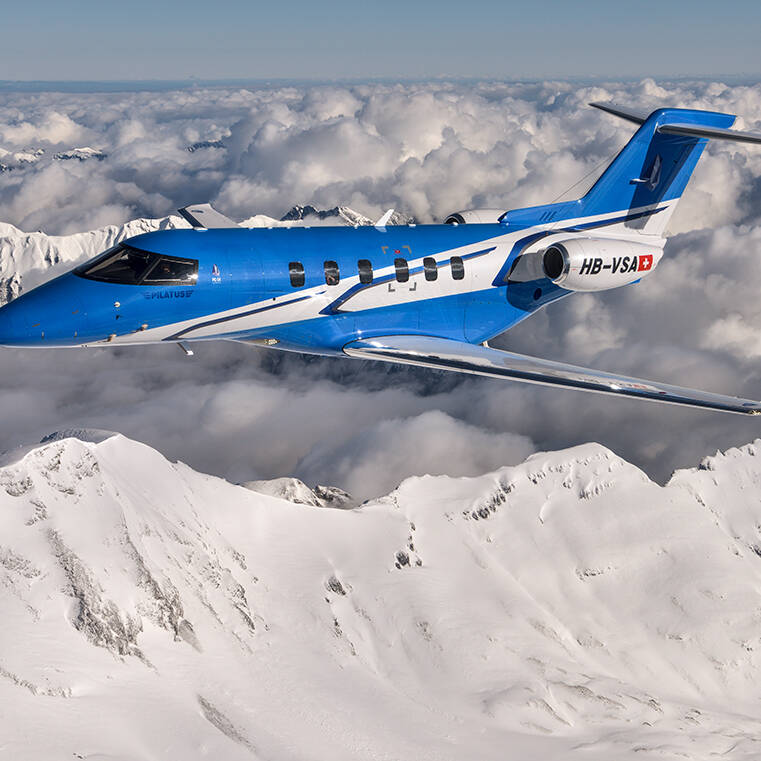
Mit Composites zu neuen Horizonten
Die neuen Businessjets PC-24 von Pilatus sind mit einem Gewicht von fünf Tonnen so leicht, dass sie auch auf kurzen Graspisten starten und landen können. Erreicht wird das geringe Gewicht durch den Einsatz von Bauteilen aus Kohle- und Glasfasern. Für deren Zuschnitt setzt Pilatus auf modernste Schneidtechnologie von Zünd.
08.10 Uhr, Fano, Mittelitalien, der PC-24 macht sich bereit für die Landung auf dem Aeroporto di Fano. Das Businessmeeting im zwei Kilometer entfernten Fano beginnt um 9 Uhr. Insofern eine ungewohnte Szenerie, als dass das Flugzeug ein brandneuer Businessjet PC-24 der Pilatus Flugzeugwerke AG und die Landebahn unbefestigt und holprig ist und gerade mal 1300 Meter misst. Üblicherweise landen Businessjets dieser Klasse im eineinhalb Autostunden entfernten Rimini, die Geschäftsfrau hätte nach der Landung noch eine längere Autofahrt vor sich gehabt.
Auf kurzen, unbefestigten Gras- und Schotterpisten zu landen, war bisher Turboprop-Maschinen vorbehalten. Seit kurzem ist das aber auch mit einem der brandneuen PC-24 möglich. Der Businessjet kann bereits nach 890 m abheben, für die Landung reichen 720 m. Das ist mitunter auf sein Basisgewicht von lediglich 5,3 Tonnen zurückzuführen. Massgeblichen Anteil an diesem niedrigen Gewicht hat die Tatsache, dass im neuen PC-24 zahlreiche Bauteile aus Karbon- oder Glasfaser verbaut werden. Für den Zuschnitt setzt Pilatus seit Jahren auf Schneidtechnologie aus dem St. Galler Rheintal. 2018 hat sich Pilatus erneut für einen hochautomatisierten digitalen Zünd Cutter entschieden.
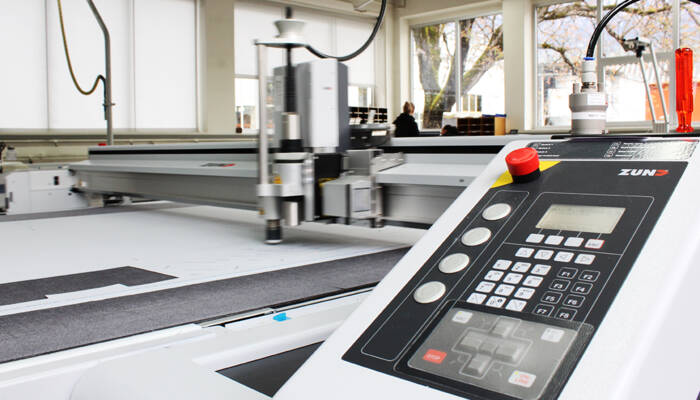
Wie baut man ein Flugzeug?
Patrick Rohrer, Projektleiter Anlagenbeschaffung bei Pilatus, weiss, was es braucht, um erfolgreiche Flugzeuge zu bauen: «Das Bekenntnis zum Produktionsstandort, die Swissness, das ist das eine. Mindestens ebenso wichtig sind hochmoderne Fertigungszellen, ausgestattet mit Spitzentechnologie» Dabei stehe die permanente Reduktion der Kosten, die Optimierung der Effizienz und die Fähigkeit, moderne Fertigungstechnologien umsetzen zu können im Zentrum.
1959 war das allerdings noch anders. Damals, als der PC-6 Porter auf dem Flugplatz in Stans zum ersten Mal abhob. Ein robustes Universalflugzeug in Ganzmetallbauweise, andere bezeichneten es auch als «Jeep mit Flügeln», vielseitig wie ein Schweizer Armeemesser. Zusammengebaut wurden die PC-6 ausschliesslich von Hand. Entsprechend erfahren mussten die Mitarbeiter sein und die Toleranzen waren grösser als heute. Der neuste Flugzeugtyp, der PC-24, besteht aus unzähligen Teilen, viel davon gefräst, mit Toleranzen im Mµ-Bereich. Der Zusammenbau erfolgt heute viel schneller, das ist nur mit modernsten Fertigungstechnologien möglich.
Seit diesem Jahr wird der PC-6 nicht mehr gebaut, nach 500 gebauten Exemplaren endet seine Erfolgsgeschichte. Der Nachfolger, der PC-12, der seit 1994 über 1650 Mal in die ganze Welt verkauft wurde, ist das heute populärste einmotorige Turboprop-Flugzeug auf dem Markt.
Schon früh wurden im Flugzeugbau erste Teile aus Kohlefaser eingesetzt. Auch beim PC-6 wurden erste GFK- und CFK-Bauteile im Handlaminatverfahren hergestellt, wenngleich noch in überschaubaren Mengen.
Im Flugzeugbau dreht sich fast alles um die Reduktion des Gewichts. Das führt dazu, dass immer mehr Teile aus Kohle- und Glasfasern gefertigt werden. Ihr grosser Vorteil ist ihre hohe Steifigkeit und Härte sowie ihre Verschleissbeständigkeit. Die Herausforderung liegt darin, die Balance zu finden zwischen Gewicht, Stabilität und Kosten. «Hinzu kommen Faktoren wie Nutzlast und Nutzraum, die so gross wie möglich sein sollen.» Noch werden bei Pilatus keine tragenden Teile aus CFK hergestellt, aber man arbeitet in der F&E intensiv daran. Beim PC-24 werden Composites hauptsächlich für Innen- und Aussenverkleidungen eingesetzt. Auch die Triebwerkverschalungen und Wingtips sind aus Kohlefaser gefertigt, sowie Fahrwerktore, Luftkanäle, diverse Rohre, Abdeckungen oder die Flügelhinterkanten.
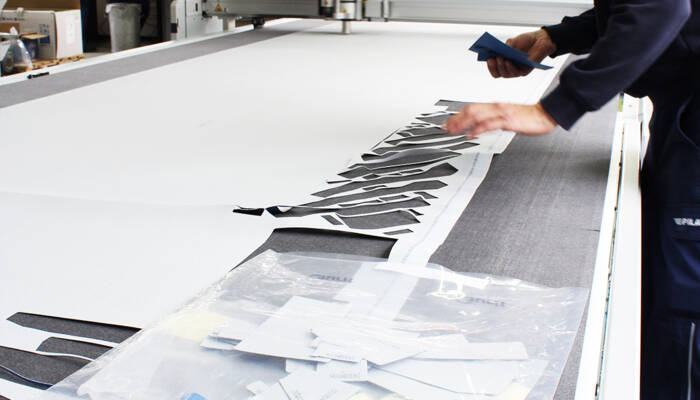
Prepregs, die Zukunft des Flugzeugbaus
Ausgangspunkt für diese Flugzeugteile sind vorimprägnierte Gewebe, sogenannte Prepregs. Dabei werden Endlosfasern imprägniert und unter Druck und Temperatur konsolidiert. Prepregs verfügen über eine hohe Festigkeit und Steifigkeit, sind ermüdungs- und verschleissbeständig, schwer entflammbar und unempfindlich gegenüber Umwelteinflüssen.
Die Prepregs werden in Rollen per Kühllaster angeliefert und bei -19 Grad im Tiefkühler zwischengelagert. Damit sie bis zum Zuschnitt Raumtemperatur erreicht haben, werden sie am Vorabend aus dem Kühler geholt. Für fünf bis 20 Tage kann das Material auf Raumtemperatur bleiben, ehe das Harz reagiert und aushärtet. Rund fünf Rollen à je ca. 90 m2 verarbeitet Pilatus täglich, etwa 90'000 m2 pro Jahr. Und der Verbrauch nimmt laufend zu; schon heute werden über die Hälfte aller in der Kunststoffabteilung gefertigten CFK- und GFK-Bauteile im neuen PC-24 verbaut. Für den Zuschnitt der Prepreg-Folien setzt Pilatus seit über 15 Jahren auf digitale Schneidtechnologie von Zünd. Nach wie vor verrichtet der Cutter aus der PN-Serie zuverlässig seinen Dienst. Mit der steigenden Nachfrage nach Bauteilen aus Kohlefaser wurde jedoch die Kapazitätsgrenze erreicht. So schneidet seit 2019 ein hochmoderner Zünd Cutter G3 L-2500 weitgehend automatisiert die einzelnen Lagen für die jeweiligen Bauteile und beschriftet sie inline mit einem integrierten Inkjetmodul.
Nach dem Zuschnitt werden die Schnittteile zu einem Kit zusammengetragen und bis zur Weiterverwendung in der Gefrierzelle zwischengelagert. Ein Bauteil kann dabei je nach Anforderungen an die Steifigkeit und Stärke aus bis zu 350 Lagen bestehen.
Für Schnittteile und deren einzelnen Lagen, für die keine DXF-Daten vorhanden sind, kommt der sogenannte Digitizer, ein Digitalisierungstisch, zum Einsatz. Vorlagen von Bauteilen können damit einfach auf dem Tisch aufgenommen und digitalisiert werden. Auch geringfügige Änderungen an Bauteilen, die vom Engineering freigegeben wurden, können mit dem Digitizer einfach angepasst und digitalisiert werden.
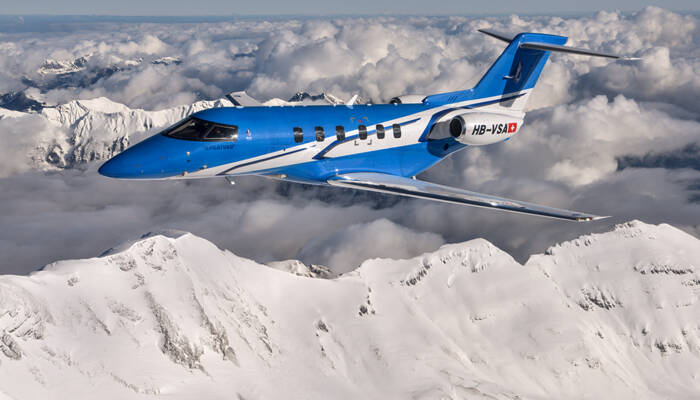
Materialeffizienz ist ein Dauerthema
Auch die permanente Optimierung der Effizienz macht den Erfolg der Pilatus aus, erklärt Patrick Rohrer. «Im Umgang mit kostenintensiven Materialien wie Kohle- oder Glasfasern ist die Materialeffizienz, respektive deren Optimierung ein Dauerthema. Wir arbeiten unablässig daran, den Ausnutzungsgrad zu erhöhen und damit auch den Abfall zu verringern. Abfall, der nach wie vor kaum wiederverwertet werden kann». Mittlerweile konnte die Abfallquote von einst 30 auf heute 20% reduziert werden. Eine wichtige Rolle spielt hier das hocheffiziente Nesting über die Software Zünd Cut Center – ZCC. Einerseits werden die Schnittteile statisch verschachtelt. Das heisst, ein Artikel, respektive seine einzelnen Lagen, werden in der Anzahl des Auftrags genestet. «Dynamisches Nesting, also das Verschachteln mehrerer Aufträge in einen Schneidjob, wird wann immer sinnvoll ebenfalls angewendet.» Dies steigert den Ausnutzungsgrad des Rohmaterials weiter.
Das Gesamtpaket ist einzigartig
Dass für die Modernisierung des Maschinenparks in der Kunststoff-Abteilung erneut Zünd den Zuschlag erhielt, ist mitunter auf gewisse Gemeinsamkeiten beider Unternehmen zurückzuführen. Und darauf, dass Zünd eine einzigartige, modulare Gesamtlösung anbietet, wie es Patrick Rohrer formuliert. Wie Pilatus bekennt sich auch Zünd klar zum Produktionsstandort Schweiz, entwickelt und produziert dort mit modernster Technologie und hochqualifizierten Fachkräften Hightech-Lösungen für die Weltmärkte. So sind denn auch die kurzen Wege ein wichtiger Faktor, die die erfolgreiche Zusammenarbeit ausmachen, betont Rohrer abschliessend. «Wir können auf 15 Jahre Erfahrung mit Schneidtechnologie von Zünd zurückgreifen, das fällt ins Gewicht. Zünd bietet offene und modulare Lösungen mit optionalen Serviceverträgen und einer extrem zuverlässigen Software ohne kurzlebige Updates. Genau das, was wir unter echtem Kundennutzen verstehen». Zünd legt enorm viel Wert auf einen perfekten Kundenservice, eine weitere Gemeinsamkeit der beiden Unternehmen.
