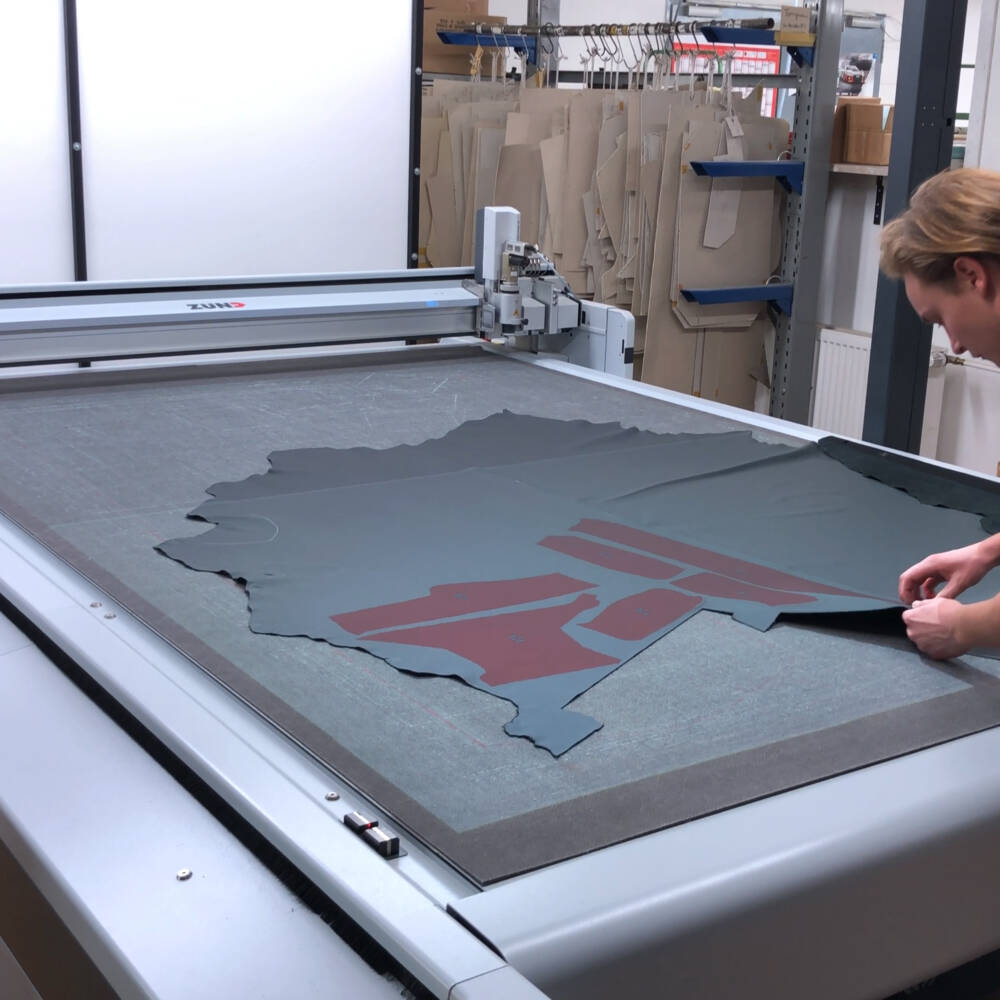
Where craftsmanship and digital cutting go hand in hand
German upholstery manufacturer Ahrndt is known for its exclusive designs in furniture and coverings. The company's automotive and furniture upholstery departments manufacture custom automotive interiors, high-end office and lounge furniture, as well as custom leather sofas – all for one-off production, very short runs, or prototyping. Ahrndt transformed its cutting operation to a digital production workflow.
Truth be told, Nina Ahrndt had a very different future in mind. After graduating from high school and completing her studies in business administration, she began working for a large company and traveled the world. It was an exciting but also very stressful time, says the young entrepreneur in conversation. She could not envision working for her parents' business in Grossbottwar, an hour's drive north of Stuttgart. But her desire for greater independence, a longing to make a difference, and her parents' urging finally won out. Since the beginning of 2017, Nina Ahrndt has been managing the family business and 20 staff members.
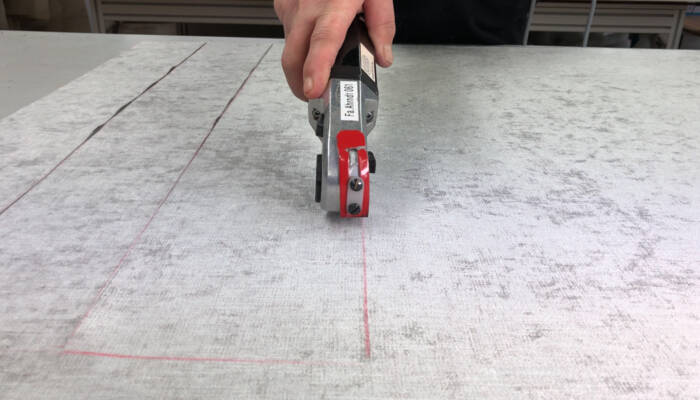
From a red dashboard to Alcantara interior panels, fireproof racing seats, and custom-made leather furniture, Ahrndt strives to satisfy almost every conceivable customer wish – unique and made to order. All products are carefully handcrafted, all materials cut by hand, the cut contours transferred onto the material with cardboard stencils. At least until the beginning of 2017, this was standard procedure. That's when Nina Ahrndt took on one of her first tasks in the family business – transforming the cutting process from analog to digital. With the increasing variety of models and variations, managing the stencils became more and more difficult, and precision cutting with shears required a great deal of skill and experience. The shortcomings of this workflow became more and more apparent.
The idea to get into digital cutting came from Gernot Ahrndt, Nina's father. As master upholsterer and founder of the company, he was consulting for a large automotive supplier that had already progressed to digital cutting with Zünd equipment. Ahrndt was so enthusiastic about the precision and performance of their Zünd cutters, he decided to invest in Zünd equipment himself.
For new developments, prototypes and the like, every millimeter counts, explains Nina Ahrndt: "In the Ahrndt Development Department, we do design and development work for many different customers. Nowadays, we cannot just send out final patterns as cardboard templates. Instead, with the touch of a button, we send them in digital form – quick and easy." If cutting patterns have to be changed and adapted, which is often the case, it is so much easier to do on a computer than with cardboard templates. In addition, material yield is a huge issue, given the high cost of leather as raw material. The cutter helps with software and a projection system, allowing us to nest cut parts as efficiently as possible to maximize material usage.
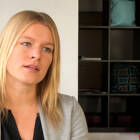
Even a company like Ahrndt, which was built on craftsmanship, cannot escape digital transformation: "We want to be able to survive in markets of the future. To do so, we need to look at digital as an opportunity and use it to our advantage," says Nina Ahrndt. Admittedly, she says, this was also a step into the unknown. How would digital cutting affect existing production workflows? Would this be the beginning of the end of crafting things by hand – of true artisanship? These initial misgivings quickly vanished: "Our employees perceive the Zünd cutter as a highly reliable and precise collaborative tool that has not taken away anyone's job. We all appreciate the advantages, the precision with which the parts are cut, which in turn facilitate the work of the saddlers and seamstresses». For example, the notches, the small triangles that mark the seam lines, are now cut into the leather with the cutter. Previously, these were manually drawn with a marker and more often than not wiped off before the parts ever reached the sewing room.
The digital process complements the handiwork – it does not abolish it; of this, Nina Ahrndt is convinced: "We can offer highly individualized products in custom sizes, unique pieces made by hand. This allows us to meet our customers' requirements better than ever before." And the company has managed to position itself differently since implementing Zünd digital cutting. Nina Ahrndt concludes: "We can offer a different level of quality and also provide cutting patterns to our customers in digital form. We have optimized our production processes and today our stock of cardboard templates is significantly reduced. Not for one second have we regretted our decision to move into the digital arena with a Zünd cutting system."
