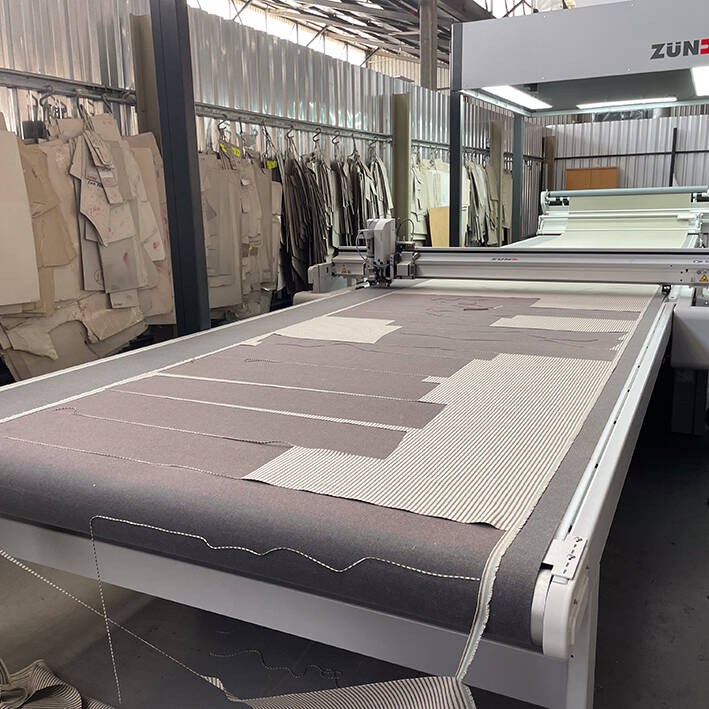
Coricraft relies on Zund
South African furniture manufacturer Coricraft is streamlining its textile processing production at its Cape Town factory with a turnkey cutting solution that includes a Zünd G3 L-2500, a high-resolution camera and intelligent MindCUT software. The installation is the only one of its kind in the southern hemisphere and one of many of its kind worldwide.
First established in 1995, Coricraft has grown from just one store in Cape Town to 42 stores across South Africa and in neighbouring Namibia and Botswana. Every Coricraft couch is built from scratch by their highly skilled team of craftsmen and women, and upholstered in either fabric or genuine leather.
In an increasingly digital production environment, order sizes are smaller, order cycles shorter, and the degree of customisation keeps increasing. Fast fashion and mass customisation are among the top industry trends. Coricraft’s latest equipment purchase allows it to process custom-printed patterned textiles, meeting changing demands in the textile industry.
Coricraft opted for the Zünd G3 L-2500 Textile Processing Solution, an 1800 x 2500mm sized digital cutting system, which enables them to do pattern matching and pattern cutting. They can now also produce prototypes much faster, whereas before, pattern matching and prototyping was done by hand.
Part of the configuration is the front and back extension tables, a textile cradle feeder at the rear, a hood with lighting for capturing the patterns with the high resolution camera, and projectors. The entire solution enables fully automated digital cutting without manual intervention, and creates an ultra-efficient workflow for Coricraft.
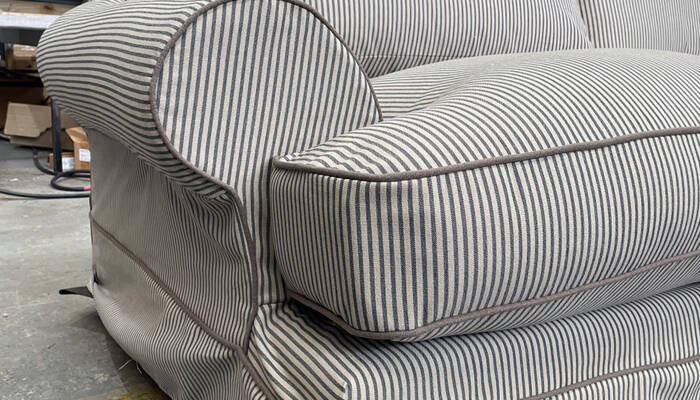
The first step of the workflow for processing Coricraft’s textiles is loading the material, with the Zünd automating material-feeding. The Canon camera then captures the fabric that needs to be digitised and its exact position and dimensions, no matter whether the material is plain or printed patterns.
The nesting software positions parts on the fabric as tightly as possible to maximise material yield and thereafter automatically creates the marker, after which textiles are notched and cut to shape with high-performance tools. The vacuum system provides reliable hold-down during the cutting process. Finally, there is unloading. The system automatically colour codes and projects other relevant data to help the operator with picking/sorting.
During the initial consultation with Coricraft, Navin Jeewanlall, Director at Midcomp, spent a day and a half at the Coricraft factory in Epping. He visited all the departments to assess processes throughout the entire factory and to get an understanding of the workflow, which initially includes design and prototyping, and thereafter when the order enters the factory, the production process, and finally when the furniture is ready for delivery.
Coricraft initially provided Midcomp with five different types of fabric to test. These were sent to Zünd in Switzerland, who made sure that the camera and software could interpret the patterns. The results were then sent back to Coricraft, who could see that the Zünd solution, in combination with the MindCUT software, could handle the materials.
Jeewanlall said that a major benefit is that the MindCUT software offers several options for pattern matching, regardless of whether part sizes need to be retained or part contours re-positioned for pattern matching. In a matter of seconds, the system makes the necessary adjustments for perfectly matching markers to the pattern at hand.
‘Part of the consultation with Coricraft was looking at how to process the cut files in CAD software correctly so that when it’s loaded onto the MindCUT software, the software can recognise reference points and know that, for example, a certain section is a back piece of a couch and another is a side piece of a couch. It can marry everything up and place it in a strategic way that when it’s cut and goes to the sewing department, the stripes, checks or whatever pattern it is, all line up. There is still sewing involved, but the lines are almost seamless, and this is what is unique about the Zünd and MindCUT solution,’ said Jeewanlall.
Jeewanlall added that the time savings for Coricraft’s couch manufacturing with the new turn-key solution are huge. ‘Prior to the Zünd being installed, Coricraft would take pieces of patterns — manual templates — place them on the fabric, and draw and cut them. Doing it this way would mean that it would take approximately two hours to nest and cut all the pieces of a particular couch. With the Zünd, we could nest and cut a 12 metre marker for one particular couch, which consisted of 35 parts, in only nine minutes.’
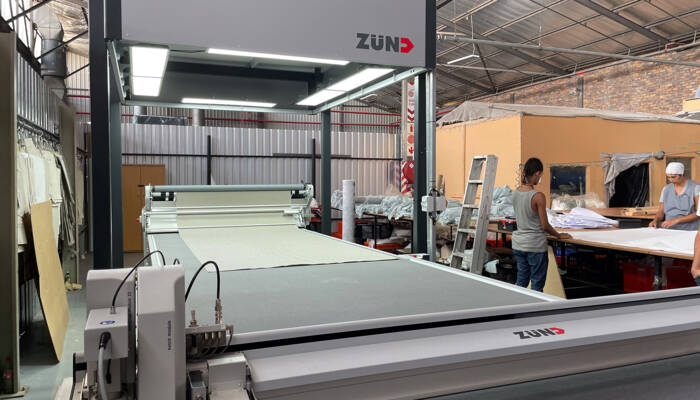
Wynand van Dyk, Production Executive at Coricraft’s Epping factory, explained how the turn-key textile cutting solution from Midcomp has helped streamline Coricraft’s production processes: ‘It has given us the opportunity to move a multitude of manual functions to automated methods. With the scarceness of trade skills, for example manual pattern matching, we can now rely on technology to assist us going forward in offering this unique fashion feature on furniture. The ability to electronically match and cut pattern fabric for decorator furniture is a first in the industry, thanks to this incredible technology.’
The cutting solution is also helping Coricraft to meet the demand for custom printed textiles. ‘Coricraft offers a made to order (MTO) offering, which creates single jobs. With this technology, we can now easily accommodate the demand from the market,’ said van Dyk.
Rolf Köppel, Segment Manager Textile at Zünd Systemtechnik, said, ‘Enabling our customers to seamlessly balance creativity with efficiency, our Pattern Matching feature revolutionises the precision of fabric cutting. By automatically recognising intricate patterns and making real-time adjustments, our software ensures that every cut is perfectly aligned, speeding production without compromising accuracy. In seconds, the system makes the necessary adjustments to perfectly match markers to the pattern at hand. MindCUT for Pattern Matching provides a complete solution for automatically aligning markers to fabric compression and stretching, including automatic pattern recognition, marker matching and cutting control.’
‘The proliferation of digital technology has had a profound impact on the textile industry. Consumers enjoy the affordability of customised clothing and upholstered furniture. With more design and configuration options available, manufacturers are streamlining their production processes through automation and increased flexibility, finding ways to successfully deal with increasing market pressures and shorter product lifecycles. With the Mind Software Suite, we offer a modular software solution that largely automates digital textile cutting — from capturing materials to creating production markers and facilitating part removal — in a well-designed, thoroughly integrated and comprehensive digital workflow,’ added Köppel.
Link to original article: https://bit.ly/3Uy5cwn
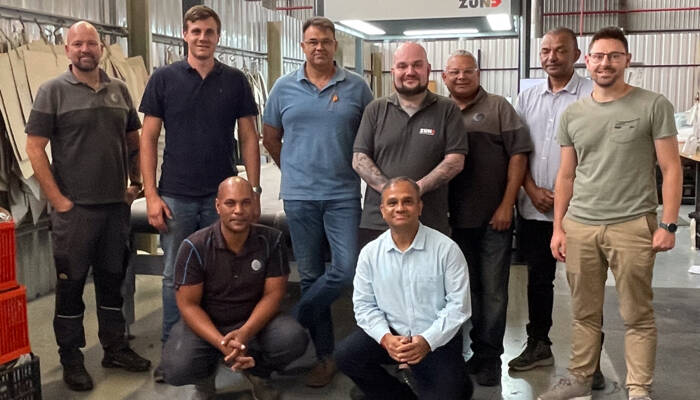