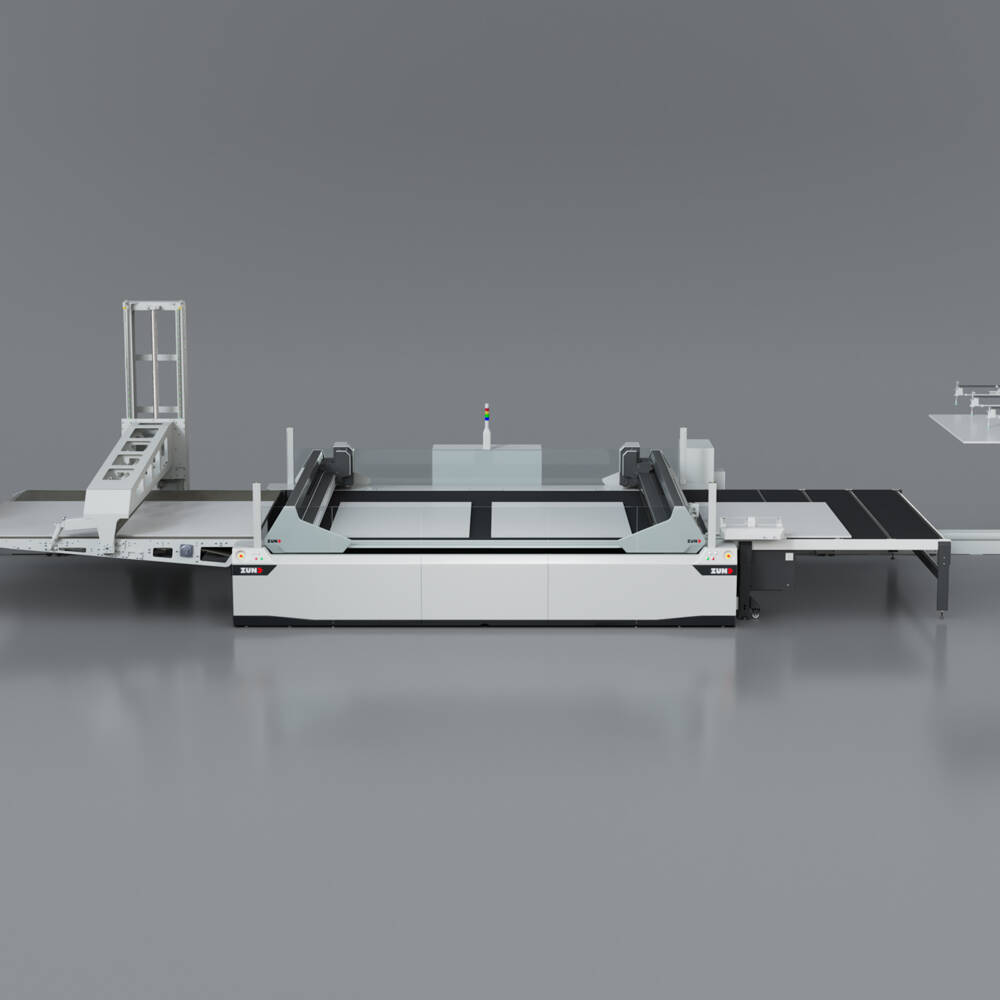
Maximize Profits and Minimize Costs
In the rapidly evolving packaging industry, companies are challenged to deliver short runs at economical prices. With digital printing, more is being printed faster than it can be cut, creating a bottleneck in the production process. To meet these demands, the Zünd Q-Line with BHS180 offers a solution that exceeds expectations and brings significant benefits to the production process: more output in less time, superior cut quality even at high speeds, reduced unit costs and higher margins.
More Output in Less Time
The Q-Line with BHS180 significantly increases production output with its dual-beam technology. The unparalleled level of automation allows operators to focus on other tasks while the machine runs completely unattended. The system's automation capabilities reduce the need for manual intervention, allowing operators to focus on more strategic tasks, ultimately increasing overall productivity. The high level of automation, combined with exceptional production capacity, ensures unmatched machine uptime. As a result, shorter production times translate into faster delivery schedules and create production buffers for more flexible production planning. The Q-Line with BHS180 ensures that even complex cutting tasks are performed with high precision and speed, which is critical to maintaining tight production schedules and meeting customer demands for short delivery times.
Reduce Unit Costs and Increase Margins
The Q-Line with BHS180 is designed to increase production value by reducing unit costs, thereby increasing profit margins. The improved price/performance ratio enhances competitiveness in the marketplace. With the Q-Line’s high level of automation and dual-beam technology for even higher performance and productivity, more parts can be produced in less time, lowering unit costs. In addition, the machine’s tight tolerances minimize material waste, reducing material costs per part. Furthermore, the Q-Line's ability to consistently produce high-quality cuts means less rework and scrap, which has a direct impact on the bottom line. Precision cutting also ensures optimal material utilization, making the production process more sustainable and cost-effective.
Flexible Production for Any Job Size
Whether producing multiple short runs or large batches, the Q-Line with BHS180 handles them all with the same efficiency and economy. The system's versatility ensures that varying order sizes can be handled without compromising on cost-effectiveness or speed. This flexibility is particularly beneficial in markets with fluctuating demand, allowing for quick adaptation without sacrificing productivity or quality.
Continuous Non-Stop Production
The integration of the BHS180, with its 1.8m stacking height, enables uninterrupted production over multiple shifts depending on the job and material. This feature allows for unattended operation, significantly reducing the need for manual intervention. The Q-Line operates at very high production speeds, maintaining exceptional die-like quality even at maximum cutting speeds. The system's ability to handle long runs without downtime increases throughput and efficiency, making it ideal for high-volume production environments. The ability to run continuously ensures that deadlines are met, even for large projects, improving customer satisfaction and reliability.
Advanced Workflow Integration
The Q-Line with BHS180 is designed for seamless integration into existing workflows, providing a scalable solution that grows with production needs. The intuitive software interface and compatibility with multi materials make it an adaptable choice for diverse production environments. This integration capability ensures minimal disruption during the transition period and allows for a quick ramp-up to full production capacity.
In conclusion, the Q-Line with BHS180 from Zünd is not just a machine; it’s a transformative solution that redefines productivity, cost-efficiency, and flexibility in digital printing and cutting systems. By incorporating this advanced system into the workflow, production capabilities are enhanced, positioning companies for greater success in the competitive packaging industry.