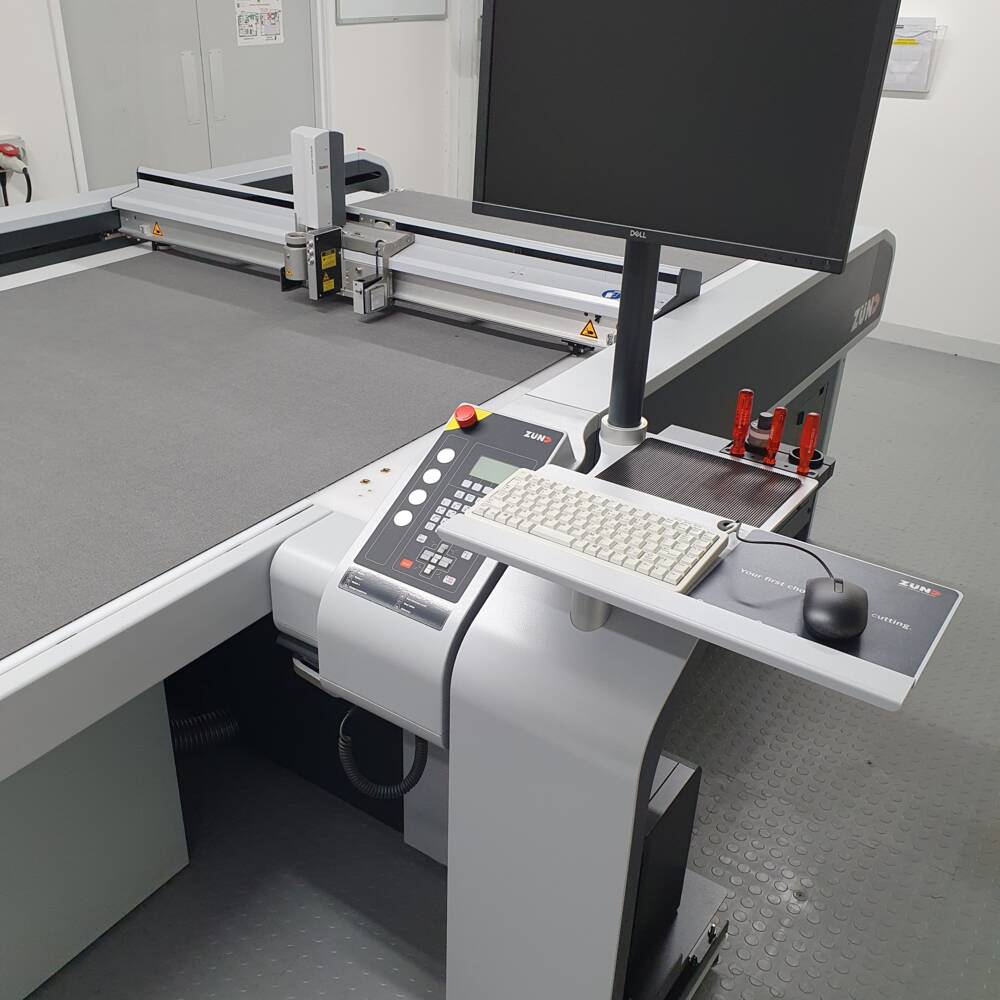
CP Composites upgrade to Zund
CP Composites was established in August 2011 in the town of Huntingdon, Cambridgeshire, an area well-known for composite laminating and motorsports manufacturing.
CP Composites began processing composite parts for the Le Mans LMP1 and LMP2 cars and as the company’s reputation for excellent service began to spread, new customers came onboard from other motorsport sectors including World Rally Championship and Formula 1. In 2015, the company moved to its current site on the Stukeley Business Centre in their hometown of Huntingdon.
Today, the company specialises in the wider automotive industry from so called ‘super cars’ to WRC and F1. However, the scope of production does not stop there. Brian Cooper Managing Director at CP Composites said, “The company has and continues to be involved with several ground-breaking innovative projects from cycling helmets to audio speakers, mono aeroplanes to bespoke prototypes.”
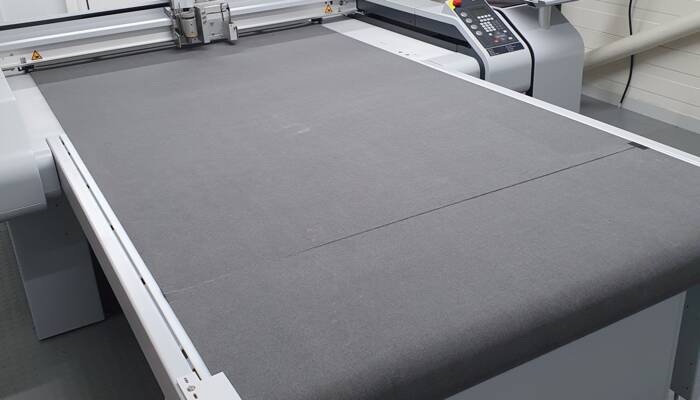
With the business progressing with more specialist work, CP Composites needed to upgrade to a faster and more advanced digital cutter. Their Exact machine was a great piece of equipment but had its limitations. Brian explains “We found ourselves getting behind in jobs and we felt we could improve on our efficiency through updated hardware and nesting software. We contacted Zund because of their relationship and understanding of our old Exact machine and decided to purchase a Zund S3 L-1600 with the help of a combined authority capital grant.”
Since the installation of the Zund S3 L-1600, CP Composites have seen huge benefits of the new Zund cutter within the business. Brian explained “Our productivity has easily improved by 20% and our material efficiency usage has never been better. We have just found so many small gains which has improved the overall process. For example, in the past we would need to visually set the blade depth and at times, ended up cutting into the bed. This created more problems because the loose belt fibres would end up cross contaminating the pre-preg materials. But now this is done by the S3 cutter using a smart Integrated Tool Initialisation function. This enables automatic blade initialisation allowing for optimum cutting depth setting, making the process far quicker and precise.”
CP Composites also opted for a front extension table on their Zund S3 L-1600which allows more working area for their operators. Brian explains “The cutting bed size on the previous Exact cutter was smaller, meaning the cutter could only process smaller pre-preg rolls and we had no working area. This made picking small composite parts very difficult. The operators at CP Composites have also found the new nesting software much faster.”