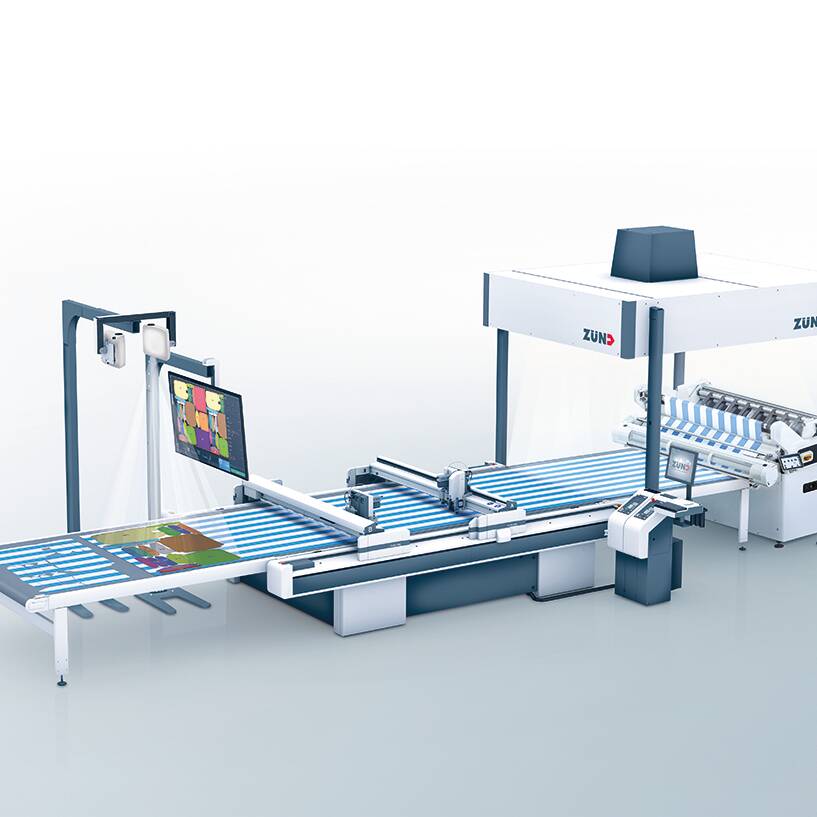
ITMA 2023 – digital expertise for single-ply cutting
Zünd will be focusing on the benefits of digital single-ply cutting in modern garment manufacturing at ITMA 2023 in Milan, Italy.
At ITMA 2023 (Hall 7, booth D303), June 8 to 14 in Milan, Italy, Zünd will be demonstrating why it is the go-to partner for customized, on-demand cutting, and why single-ply cutting of fabrics offers nothing but advantages. Digital technologies are changing the garment industry Manufacturers are dealing with rapidly advancing digitalization along with increasingly short product life cycles by investing in lean and highly automated production workflows. Zünd solutions allow them to rationalize processes from ordering to cutting while minimizing manual interventions.
Digital, automated single-ply cutting is the answer to these new production realities. Zünd’s single-ply cutters are the perfect cutting tools for production-workflow automation, offering manufacturers the flexibility and profitability they so urgently need. Intelligent automation features, optical solutions, and software tools make it easier for them to optimize their resources, monitor material usage, and support employees, so they can focus on other activities that add greater value to the business. With digital, single-ply cutting technology, manufacturers can increase productivity while expanding their production capacity. With very economical and efficiently scalable on-demand production, manufacturers can easily accept last-minute orders and meet short delivery times. They can handle spikes in demand with ease and confidence.
Zünd cutters combine tremendous versatility in a single machine, giving users access to a completely new level of flexibility in their production workflow. They can process demanding textiles, complicated patterns, and diverse shapes without any difficulty. Zünd’s cutting technology allows the garment industry to produce customized, made-to-measure clothing in small batches and on demand just as economically and efficiently as large quantities. It enables processing and handling multiple orders more quickly while simultaneously saving both time and material with highly efficient nesting capabilities. Combining this technology with MindCut production software and the superior precision of single-ply cutting leads to almost zero waste. Parts can be nested very tightly and close to the edges of the material, which generates considerable savings but also helps reduce the environmental footprint.