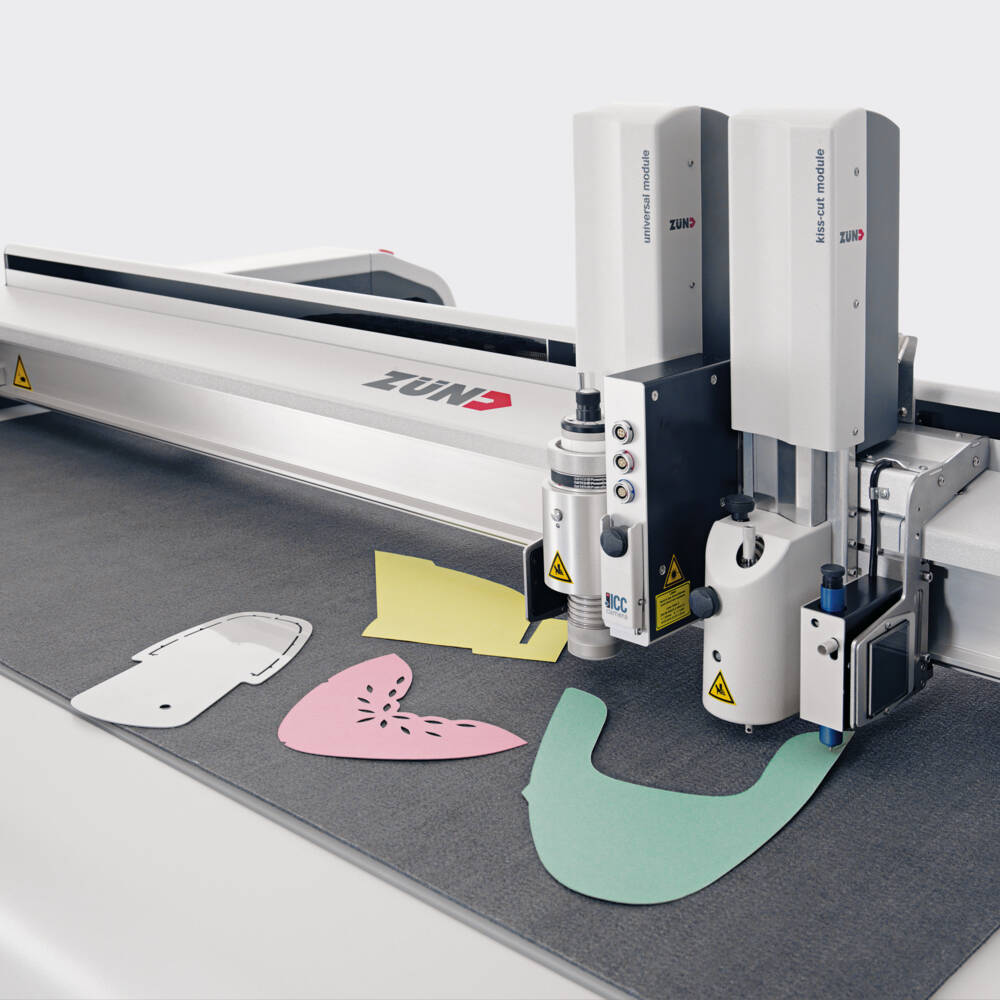
Zünd at SIMAC – innovative cutting technology for leather and textile
At Simac in Milan, Zünd will be presenting innovative solutions for digital leather and textile cutting, including interactive nesting with mixed-reality glasses and a very compact Zünd G3 cutter equipped for processing leather. These and the many other exciting new production methods on display at Booth K9/K17 in Hall 18 are laying the groundwork for the Smart Factory.
For the cutting process, Zünd offers a compact cutting system ideally suited to the specific technical requirements of the leather-processing industry. The Zünd G3 cutter with back extension offers a 227 x 280 cm / 89 x 110 in working area. This compact G3 configuration provides plenty of space for nesting, cutting, and removal of parts on a single cutter along with unparalleled production efficiency. The working area is perfect for processing up to medium-sized hides and yet so compact that even small cut parts can be removed with ease. Cutter operation, hide infeed, and parts nesting are handled centrally from the front of the cutter for maximum user-friendliness. The cutting workflow goes from front to back and is divided into three sections for loading, cutting, and parts removal. This makes it possible to place and grade a new hide and remove finished cut parts, all while cutting is underway, which eliminates downtime and significantly boosts productivity. The Zünd cutter is controlled via the Mind production software and can accommodate three tools.
Interactive nesting with augmented reality
All steps in the cutting workflow are controlled with Mind software, as is the interactive nesting function, which is carried out using Augmented Reality glasses. This patented workflow enables software-aided nesting in addition to purely manual and fully automated parts placement. Using the mouse, the operator can turn, arrange, and place parts on the leather or fabric as needed, according to specific nesting criteria.
In this context, parts nesting with mixed-reality glasses as an interactive tool is sure to garner plenty of attention. Together with software partner Mind, Zünd will be giving live demonstrations of how the nesting process can be made even more efficient with this mixed-reality technology. One major advantage is that even materials with treated, shiny surfaces can be marked with ease. Conventional projection solutions struggle with such surfaces.
In addition, Zünd, as a total solution provider in the field of digitized leather processing, is pleased to announce its exclusive partnership with Mindhive Global, the leader in automated leather grading with precision and pace, at scale to develop finished leather grading with.
Feature recognition for textile applications
The Feature Recognition software function detects motifs as well as different parts of a garment so that it can position them on the fabric with the utmost precision for subsequent cutting. This saves valuable time in job preparation. In fact, the process is completed in the blink of an eye by selecting the model, entering the motif properties, and positioning the individual cut parts. The software captures their positions and repeats them along the length of fabric. Cutting can then begin immediately. Feature Recognition automates what has, until now, always been a time-consuming, manual process. It enables extremely high repeatability and therefore fulfills the most stringent quality requirements, particularly in the luxury segment.
Automated roll management with the new Roll Handling System – RHS6-50
The brand-new Roll Handling System – RHS6-50 is a game changer for uninterrupted cutting on an industrial scale. The system can hold up to six rolls of textiles weighing 50 kg each. Depending on the job, they can be identical or different types of fabric. The large, fully automated Roll Handling System delivers significantly longer uninterrupted cutting times. The RHS6-50 supplies the Zünd cutter with material completely autonomously. This enables extremely long production runs, during which operator interventions are no longer needed. The only remaining manual task is loading the rolls onto the RHS. As part of this process, the operator scans the barcodes of the individual rolls. The material assignment and the RHS6-50 are controlled directly with MindCUT software.