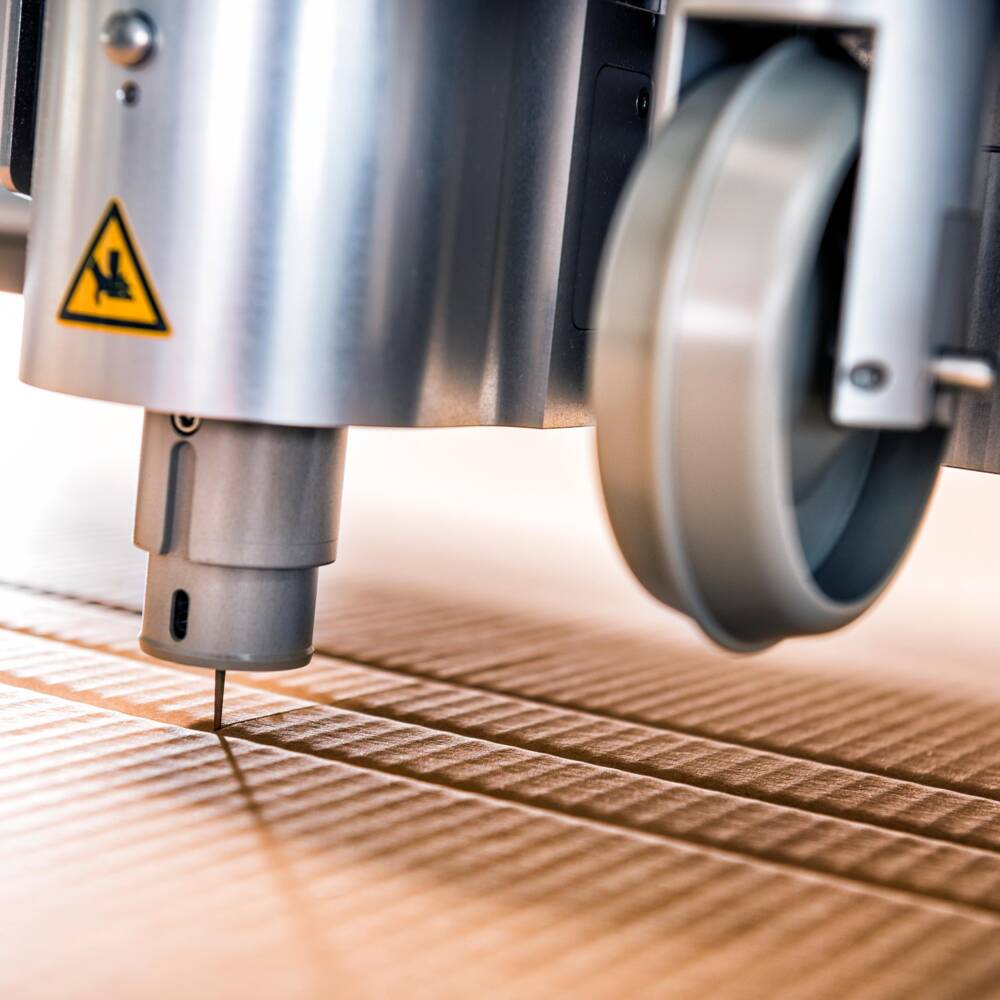
A standout example of digital packaging production
In the course of 30 years, Zerhusen Kartonagen GmbH has evolved from a small packaging supplier to one of Germany's largest manufacturers and converters of corrugated cardboard. The family business was quick to recognize the potential of digital technologies and knows how and where to implement them profitably. The most recent milestone was the opening of a new development center furnished with the latest Zünd cutting equipment.
The packaging market is changing. Digital automation plays a huge role in this. Zerhusen Kartonagen is a great example of how packaging manufacturers are adapting to new demands in the marketplace. Early on, the company began to pivot to digital equipment and workflows which have made it leaner and more efficient. Customer requirements have been changing in recent years, explains Hermann Kage in an interview. Kage heads up the company's development team and knows what customers want: “In the past, customers demanded packaging for their products that, first and foremost, had to be inexpensive and easy to use. In most cases, this meant a simple folding box. These days customers bring their product to us and order tailor-made packaging for it, including protective interiors. All made of corrugated cardboard, needless to say."
More and more customers value a thorough, attractive presentation of their prototypes. In addition, as the company's customer base grows, so do the requests for more specialized packaging. Sampling has, therefore, become an important benchmark in product development. In the end, only professionally finished packaging provides the customer with the true look and feel of the end product.
With changing customer requirements, customer support has become even more important at Zerhusen, prompting further expansion of consulting and development capacities. Lean but smart packaging concepts are very much in demand today. In response to these trends, Zerhusen Kartonagen opened a new development center at the beginning of 2020, which constitutes the new base of operations for Kage and his team of four. The center occupies a 1,250 m² space with state-of-the-art samplemaking facilities, offices, and meeting rooms for customer presentations. "Our job is to develop innovative and creative concepts for new packaging and present these prototypes to our customers."
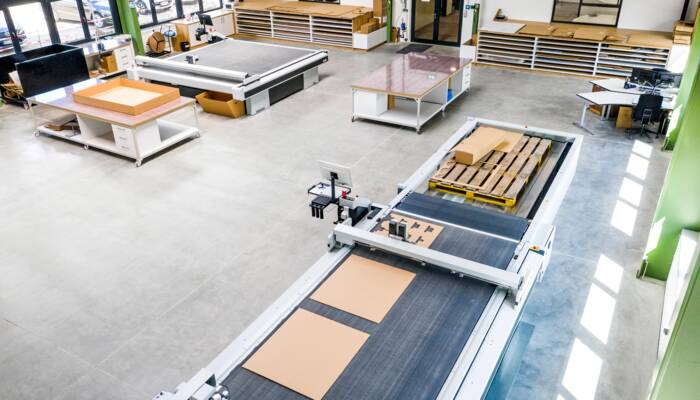
From small business to industry leader
The history of the family business begins in 1987, with a three-man enterprise. Today Zerhusen employs 550 people, has an annual turnover of 100 million euros, and is one of the largest corrugated board converters in Germany. Initially, the company dealt in finished packaging and took care of the warehousing and logistics for its customers, one of the first providers to offer these services. In the following years, the offerings continued to expand, step by step. In the early 1990s, the company started its own converting operation and packaging production. And at the same time, it also started providing samplemaking services. Since 2016 Zerhusen has also been producing its own corrugated cardboard, at a rate of more than 200 million m² per year.
Warehousing and logistics of packaging are in greater demand than ever, despite, or perhaps because of, the trend towards on-demand production and just-in-time delivery. “We supply packaging for numerous online businesses. With the continued growth in e-commerce, there has been a considerable uptick in demand for packaging. Our recipe for success is easy, quick, and flexible delivery. " If you order by 4 p.m., we provide next-day delivery – made possible by two fully automated high-bay warehouses with six aisles and 50,000 product slots as well as our own fleet of delivery vehicles. These days, Zerhusen supplies customers in the furniture, automotive, food, and plastics industry within a 350-km radius.

All-in-one samplemaking and production cell
Zerhusen invests heavily in new technologies and state-of-the-art production equipment. This has also opened the door to new business opportunities. In the past, the company dealt exclusively with smaller, regional companies. Now Zerhusen serves primarily a large, industrial clientele. "Here in the Oldenburger Münsterland, many small businesses have grown up, and so have we". Zerhusen is located in Damme in Lower Saxony, a 30-minute drive north of Osnabrück, a region that has benefited from becoming industrialized. An environment that is reorienting and reinventing itself through digital transformation. Much like Zerhusen Kartonagen. There are two state-of-the-art digital cutting systems from Swiss manufacturer Zünd operating in the company's development center. A Zünd G3 L-3200 cutter, in use since 2012, was upgraded with an automated material-handling solution in early 2020. At the same time, a Zünd G3 3XL-3200 was installed, configured especially for initial prototyping.
The fact that one of the Zünd cutters was retrofitted with BHS Board Handling shows that these cutting systems are not only used for samplemaking: “The two Zünd cutters are more than just samplemakers. In most cases, we don't just create one or two packaging samples for our customer presentations. We frequently produce up to 40 additional samples that are palletized as part of the testing process. In addition, we are increasingly producing short runs digitally these days. With our Zünd cutters, short-run digital production has become an attractive business proposition. And at the same time, the Zünd cutters have also opened up new possibilities in sample production. We are quite a bit more flexible these days».
Rather unusual for a design and development department is the high-bay warehouse that stores dozens of different types of corrugated board. This is so every sample package is made with exactly the same cardboard that will be used in production.
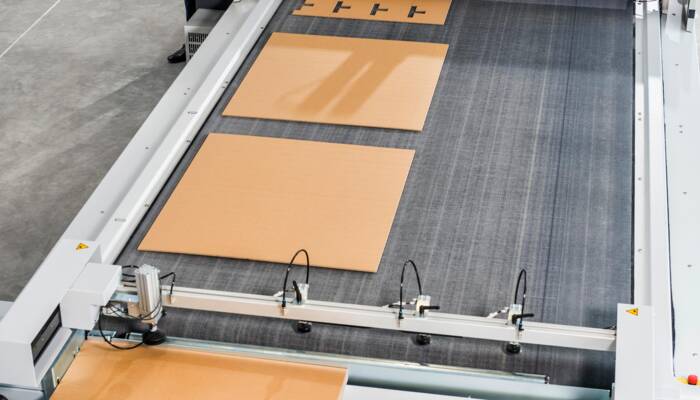
The digital revolution continues
According to Kage, besides their cutting accuracy and legendary reliability, Zünd's modular design was an important factor in their decision-making process: “The subsequent upgrade of the existing Zünd cutter with an automatic BHS Board Handling System was impressively quick and simple. And in Zünd, we have a partner in digital cutting who is continually developing new technologies and bringing new tools to market that we can add to our Zünd equipment very quickly—be it the V-Cut Tool or the new PCT Press Cutting Tool. For packaging that is to be cut on a large rotary or flat-bed die cutter, we can simulate the same processes on the Zünd. And with the tools Zünd offers, the Press Cutting Tool PCT for instance, or the scoring wheels, we are able to do this very well in very close approximation to traditional die-cut standards. That makes Zünd cutters unique».
But Zerhusen Kartonagen spends no time resting on its laurels. 6 months after modernizing its cutting operations, the company's verdict is positive through and through: “The stated goal for our investment in Zünd digital cutting technology was to further increase customer satisfaction, gain new customers, and be able to serve our customers even more quickly and flexibly. We have met these targets, but the digital transformation continues. Our Zünd cutters still offer a lot of potential for further optimization».
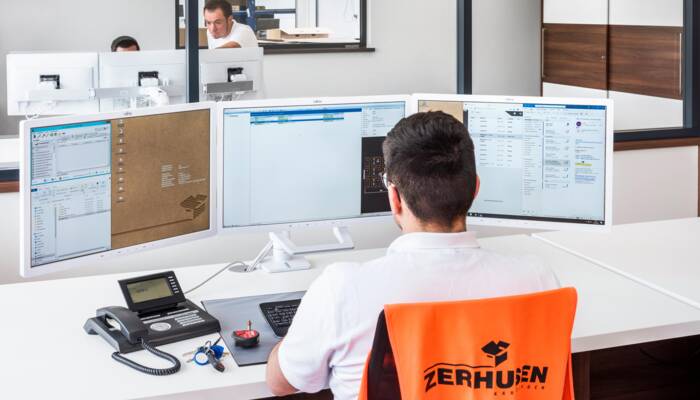