
Holroyd Components invest in their seventh Zund cutter
The Essex based company have added another Zund cutter to their ever-growing Zund fleet to support the ever-increasing demand for electric heating elements.
Holroyd Components Ltd have been manufacturers of industrial electric heating elements since 1972, specialising in bespoke flexible silicone heater mats that can heat up to 250 degrees Celsius.
Fast approaching their 50th anniversary next year, the company has always followed their ethos of using high-quality materials, continual investment in new machinery and providing first-class customer service. This in return has allowed them to maintain their long-standing presence as Europe’s market leader in surface heating systems.
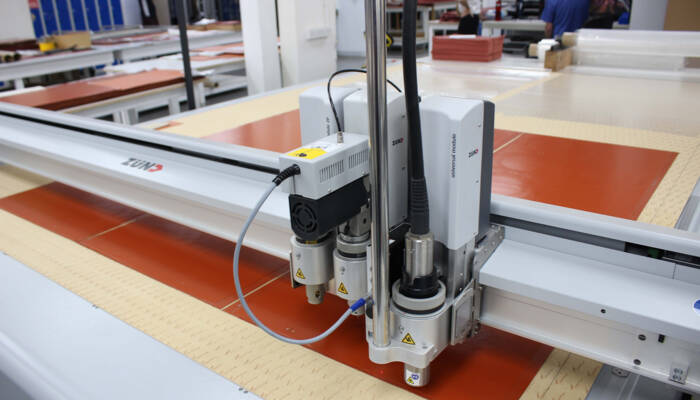
Andy Fitzpatrick, Technical Manager at Holroyd Components explained “To maintain the high standard of quality and service that our customers have come to expect, Holroyd Components Ltd have an ongoing programme of investment in plant, machinery and resources. This has enabled us to offer high-quality products, in accordance with an ISO9001:2015 Quality System with a fast, flexible and efficient delivery for both small quantities and large batch orders”.
Holroyd Components bought their first Zund G3 Digital Cutter in 2015 as part of a manufacturing process transformation. They have moved away from hand and die cutting the final shape of the silicone heater to using the latest Zund, digital cutting automation. The company quickly recognised the benefits of using Zund cutting technology for their design and production, and as a result, an S3 cutter quickly followed for the cutting of their silicone raw materials. Andy explains “In the past we used to hand cut the silicone glass fibre laminate using a metal template and a Stanley knife. This process was very time consuming and maintaining the accuracy was very challenging. For example, on each job there would be time spent finding the correct template and the accuracy was dependant on the persons experience. Sometimes people would cut themselves, causing more delays in the production runs. We knew we needed to move with the times and decided to purchase a Zund cutter, which we had been considering for a while”.
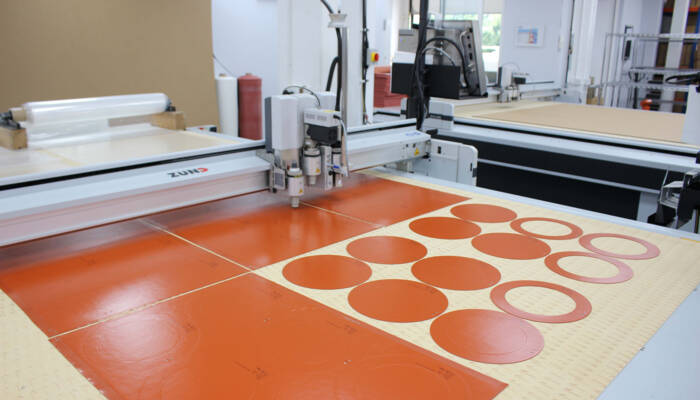
Digitising their cutting process has revolutionised the company’s manufacturing process and benefited Holroyd Components in other ways. Andy explains “Once we would hand-cut the finished heater to size or used die cutting blades to cut the more intricate final shapes. We now use the large Zund G3 XL-3200 cutter for this and save so much on time and cost. In the past we used to outsource the tooling of the cutting dies for each job and store them in our warehouse for up to 2-years in-case there was another order from the same customer. The saving in time and warehouse space does make a significant impact, especially when we are producing 30 plus bespoke designs everyday”.
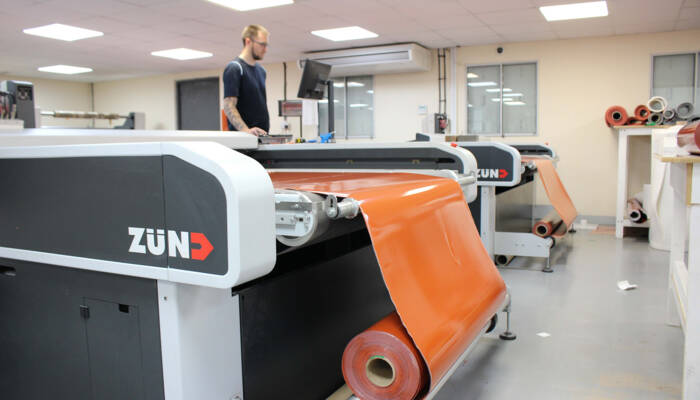
Holroyd Components have today grown their Zund fleet to seven cutters all doing a variety of jobs as part of the manufacturing process. The company bought their latest Zund G3 XL-3200 in March 2021 to increase production capacity. Andy explains “The versatility of the Zund cutters is exceptional, hence we keep purchasing more cutters. In the past we would have different processes for roll cutting, intricate final cuts and drilling pin boards. The Zund cutters have absorbed all the different processes and reduced the need to move materials between different machinery. For example, three of the G3 cutters have the Leibinger part marking system, making a separate printer redundant. We used to hand drill pin boards using a rigid jig but now we have a router installed on our G3 M-2500 which drills the small holes for us. As our silicone heaters can be any shape or size, our packaging sizes also need to be flexible, so we use the G3 machines to cut and crease cardboard sheets to make our bespoke shipping boxes. Our manufacturing has evolved so much with the use of Zund technology; and we will remain loyal to the brand for many years to come.”