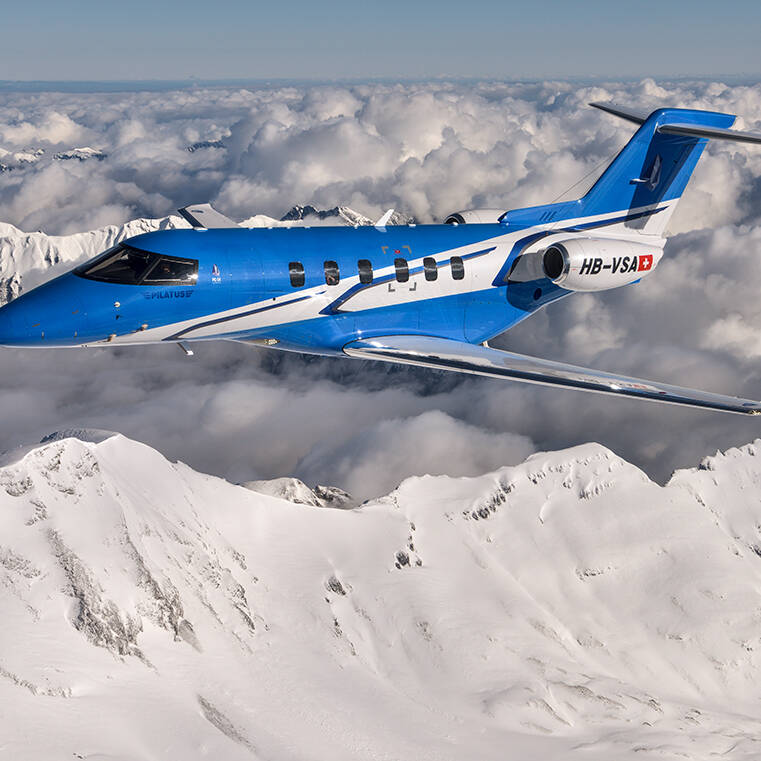
Met composieten naar nieuwe horizonten
De nieuwe zakelijke jets PC-24 van Pilatus zijn met hun gewicht van vijf ton zo licht dat zo ook op korte grasbanen kunnen starten en landen. Het geringe gewicht wordt bereikt door het gebruik van componenten van koolstof- en glasvezel. Voor het snijden vertrouwt Pilatus op de zeer moderne snijtechnologie van Zünd.
08:10 uur, Fano, midden-Italië, de PC-24 maakt zich klaar voor de landing op het Aeroporto di Fano. De zakelijke bespreking in het twee kilometer verderop gelegen Fano begint om 9 uur. Dit is daarom een ongebruikelijk schouwspel omdat het vliegtuig een hagelnieuwe zakelijke jet PC-24 van Pilatus Flugzeugwerke AG is en de landingsbaan onverhard en hobbelig is, met een lengte van slechts 1300 meter. Gewoonlijk landen zakelijke jets van deze klasse in het anderhalf uur rijden verderop gelegen Rimini en had de zakenvrouw na de landing nog een lange autorit moeten maken.
Op de korte, onverharde gras- en steenslagbaan landen was tot voor kort alleen voorbehouden aan turbopropmachines. Sinds kort is dat echter ook mogelijk met de hagelnieuwe PC-24. De zakelijke jet kan al na 890 m opstijgen, voor de landing zijn 720 m genoeg. Dat is mogelijk dankzij het basisgewicht van slechts 5,3 ton. Maatgevend aandeel in dit lage gewicht zijn de talloze componenten van koolstof- en glasvezel die in de nieuwe PC-24 zijn ingebouwd. Voor het snijden daarvan vertrouwt Pilatus al jarenlang op snijtechnologie uit het Rijndal van St. Gallen. In 2018 heeft Pilatus gekozen voor een zeer geautomatiseerde digitale snijmachine van Zünd.
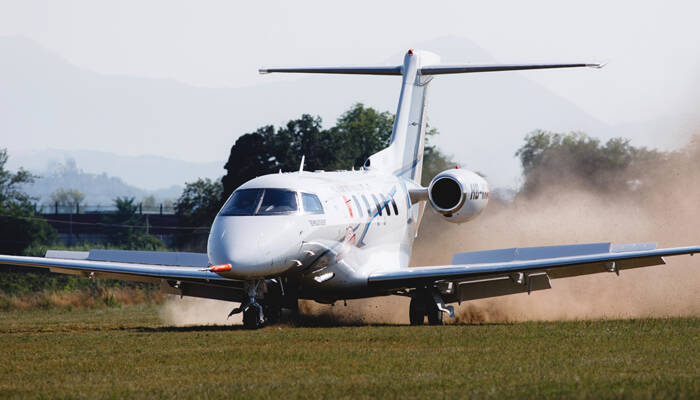
Hoe bouw je een vliegtuig?
Patrick Rohrer, projectleider installatieaanschaf bij Pilatus, weet wat er nodig is om succesvolle vliegtuigen te bouwen: 'De bekendheid met de productielocatie, de Zwitsersheid, dat is één ding.Minstens zo belangrijk zijn ultramoderne fabricagecellen, uitgerust met toptechnologie.' Daarbij staan de permanente vermindering van de kosten, de optimalisering van de efficiëntie en de mogelijkheid om moderne fabricagetechnologieën te kunnen toepassen centraal.
In 1959 was dat nog heel anders. Toen steeg de PC-6 Porter voor het eerst op van het vliegveld van Stans. Een robuust universeel vliegtuig dat geheel van metaal was gemaakt. Het werd ook wel 'een jeep met vleugels' genoemd, veelzijdig als het Zwitserse zakmes. De PC-6 werd helemaal met de hand gebouwd. De medewerkers moesten dan ook zeer ervaren zijn, en de toleranties waren groter dan nu. Het nieuwste vliegtuigtype, de PC-24, bestaat uit talloze onderdelen, veel daarvan gefreesd, met toleranties in het Mµ-bereik. De bouw gaat nu veel sneller, dat is alleen mogelijk met zeer moderne fabricagetechnologieën.
Sinds dit jaar wordt de PC-6 niet meer gebouwd, na 500 exemplaren eindigt zijn succesverhaal. De opvolger, de PC-12, die sinds 1994 al 1650 keer over de hele wereld is verkocht, is momenteel het populairste eenmotorige turboprop-vliegtuig op de markt.
Al snel worden in de vliegtuigbouw de eerste onderdelen van koolstofvezel gebruikt. Ook bij de PC-6 werden de eerste GFK- en CFK-onderdelen gebruikt, handmatig als aminaat gemaakt, zij het nog in overzichtelijke hoeveelheden.
In de vliegtuigbouw draait bijna alles om een zo laag mogelijk gewicht.Dat leidt ertoe dat steeds meer onderdelen gemaakt worden van koolstof- en glasvezel. Deze hebben als groot voordeel hun hoge stijfheid, hardheid en slijtbestendigheid. De uitdaging ligt erin om de balans te vinden tussen gewicht, stabiliteit en kosten. 'Daarbij komen factoren als nuttige last en gebruiksruimte, die zo groot mogelijk moeten zijn.' Nu nog worden bij Pilatus geen dragende delen van CFK gemaakt, maar daar wordt bij de afdeling O&O hard aan gewerkt. Bij de PC-24 worden composieten hoofdzakelijk gebruikt voor binnen- en buitenbekleding. Ook de transmissiehuizen en vleugeltips zijn gemaakt van koolstofvezel, net als de onderstelkleppen, diverse buizen, kappen en vleugelachterkanten.
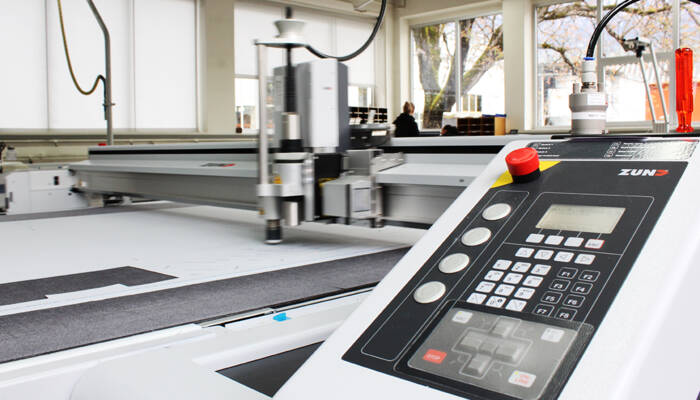
Prepregs, de toekomst van de vliegtuigbouw
Uitgangspunt bij deze vliegtuigonderdelen zijn voorgeïmpregneerde weefsels, zogenaamde prepregs.Daarbij worden doorlopende vezels geïmpregneerd en onder druk en temperatuur geconsolideerd. Prepregs beschikken over een hoge vastheid en stijfheid, zijn bestand tegen vermoeidheid en slijtage, branden slecht en zijn niet gevoelig voor omgevingsinvloeden.
Prepregs worden in koelwagens in rollen aangeleverd en bij -19 graden in de diepvries opgeslagen. Om ervoor te zorgen dat ze bij het snijden op kamertemperatuur zijn, worden ze de vorige avond uit de koeling gehaald. Gedurende vijf tot twintig dagen kan het materiaal op kamertemperatuur blijven totdat de hars gaat reageren en uitharden. Pilatus verwerkt ongeveer vijf rollen van elk ong. 90 m² per dag, zo'n 90.000 m² per jaar. Dit verbruik neemt voortdurend toe; nu al wordt meer dan de helft van alle in de kunststofafdeling gemaakte CFK- en GFK-componenten in de nieuwe PC-24 ingebouwd. Voor het snijden van de prepreg-rollen vertrouwt Pilatus al 15 jaar op de digitale snijtechnologie van Zünd. Net als eerder doet de snijmachine uit de PN-serie betrouwbaar haar werk. Met de stijgende vraag naar componenten van koolstofvezel werd echter de capaciteitsgrens bereikt. Daarom snijdt sinds 2019 een ultramoderne Zünd-snijmachine G3 L-2500 grotendeels automatisch de verschillende lagen voor de componenten en beschrijft deze inline met een geïntegreerde inkjetmodule.
Na het snijden worden de snijdelen samengevoegd tot sets en tot hun verdere verwerking opgeslagen in de vriescel. Een component kan daarbij, afhankelijk van de vereisten aan stijfheid en dikte, uit wel 350 lagen bestaan.
Voor snijdelen en de individuele lagen ervan waarvoor geen DXF-gegevens beschikbaar zijn, wordt de zogenaamde digitizer, een digitaliseringstafel, gebruikt. Sjablonen van componenten kunnen daarmee eenvoudig op de tafel worden geplaatst en gedigitaliseerd. Ook minimale veranderingen aan componenten die door de technische afdeling zijn vrijgegeven, kunnen met de digitizer eenvoudig aangepast en gedigitaliseerd worden.
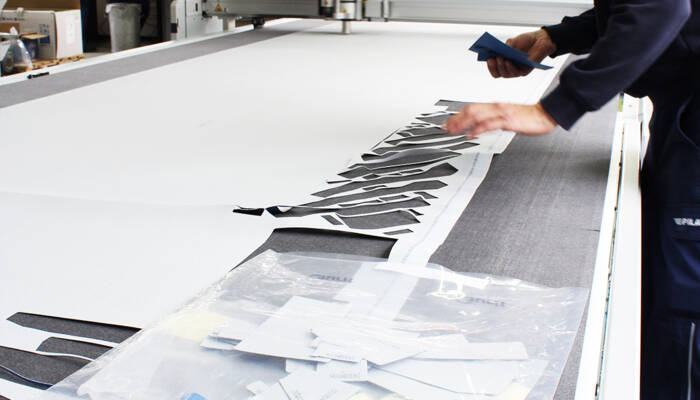
Materiaalefficiëntie is voortdurend van belang
Ook de permanente optimalisatie van de efficiëntie draagt bij aan het succes van de Pilatus, verklaart Patrick Rohrer.'In de omgang met kostenintensieve materialen zoals koolstof- en glasvezels is het materiaalrendement, respectievelijk de optimalistatie ervan, voortdurend een thema. Wij werken onafgebroken eraan om de benuttingsgraad te verhogen en zo voor minder afval te zorgen. Afval dat net als vroeger nauwelijks nog verder bruikbaar is.' Inmiddels is het afvalpercentage van ooit 30 tot nu 20% verminderd. Een belangrijke rol hierbij speelt het zeer efficiënte rangschikken met de software Zünd Cut Center, ZCC. Aan de ene kant worden de snijdelen statisch genest. Dat wil zeggen dat een artikel, of de individuele lagen ervan, in het aantal van de opdracht worden gerangschikt. 'Dynamisch rangschikken, het nesten dus van meerdere opdrachten in één snijtaak, wordt wanneer ook maar mogelijk zinvol ingezet.' Dit vergroot de benuttingsgraad van het ruwe materiaal verder.
Het totaalpakket is uniek
Dat voor de modernisering van het machinepark in de kunststofafdeling opnieuw Zünd de voorkeur kreeg, is te verklaren uit bepaalde gemeenschappelijke kenmerken van beide bedrijven.En wel doordat Zünd een unieke, modulaire totaaloplossing biedt, zoals Patrick Rohrer het noemt. Net als Pilatus kiest Zünd bewust voor Zwitserland als productielocatie en ontwikkelt en produceert daar met de modernste technologie en hoogopgeleide vakkrachten hightech-oplossingen voor de wereldmarkt. Zo zijn ook de korte afstanden een belangrijke factor die voor een succesvolle samenwerking zorgt, benadrukt Rohrer tot besluit. 'Wij kunnen teruggrijpen op 15 jaar ervaring met snijtechnologie van Zünd, dat legt gewicht in de schaal. Zünd biedt open en modulaire oplossingen met optionele serviceovereenkomsten en extreem betrouwbare software zonder voortdurende updates. Dat is precies wat wij onder klantgerichtheid verstaan.' Zünd hecht bijzonder aan een perfect klantenservice, opnieuw iets wat beide bedrijven gemeen hebben.
