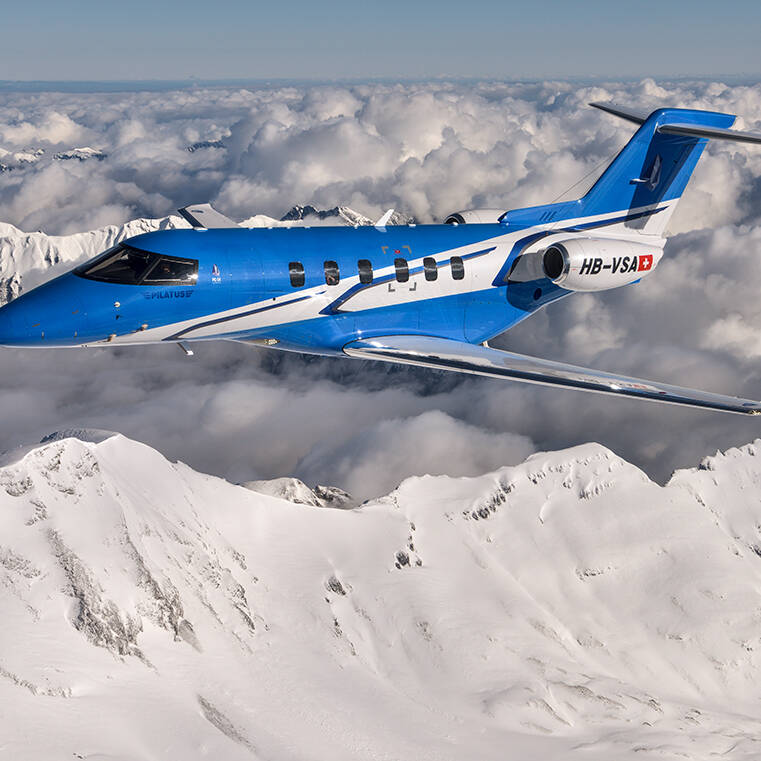
Usando compósitos para alcançar novos horizontes
Pesando cinco toneladas, os novos jatos executivos PC-24 da Pilatus são tão leves que podem decolar e pousar mesmo em pistas curtas não pavimentadas. O baixo peso é alcançado graças ao uso de componentes feitos de carbono e fibras de vidro. Para isso, a Pilatus conta com a tecnologia de corte de última geração da Zünd.
08h10, Fano, Itália, o PC-24 está se preparando para pousar no Aeroporto de Fano. A reunião de negócios em Fano, a dois quilômetros de distância, começa às 9 horas da manhã. Esta é uma cena incomum, pois a aeronave é um novo jato executivo PC-24 da Pilatus Flugzeugwerke AG. A pista não pavimentada e irregular, mede apenas 1300 metros. Normalmente, jatos executivos dessa classe pousam em Rimini, a uma hora e meia de carro, ou seja, a empresária teria uma viagem mais longa pela frente após o pouso.
O pouso em pistas curtas e não pavimentadas de grama e cascalho era anteriormente reservado apenas para aeronaves de hélice. Mas isso passou a ser possível, recentemente, com as novas aeronaves PC-24. O jato executivo pode decolar após apenas 890 m, e 720 m são suficientes para o pouso. Isto acontece graças ao seu peso base de apenas 5,3 toneladas. Essa leveza é em grande parte porque o novo jato PC-24 é equipado com inúmeros componentes feitos de fibra de carbono ou vidro. Durante anos, a Pilatus conta com a tecnologia de corte do Vale do Reno de St. Gallen para o corte. Em 2018, a Pilatus mais uma vez optou por uma mesa de corte digital da Zünd altamente automatizada.
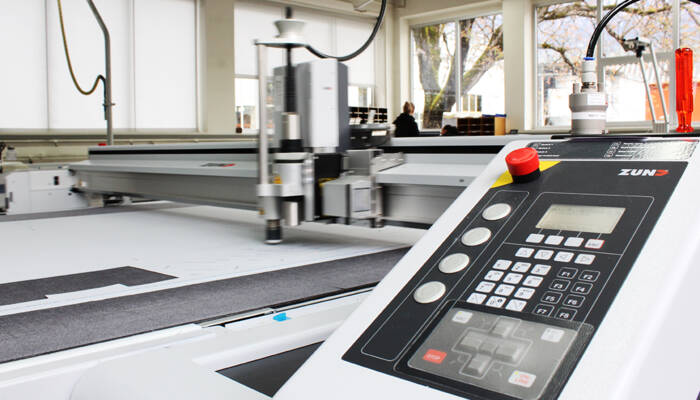
Como se fabrica um avião?
Patrick Rohrer, Gerente de Projetos de Compras de Fábrica da Pilatus, sabe o que é preciso para construir aeronaves de sucesso: "O compromisso com a produção na Suíça, isso é um fator importante. Pelo menos tão importante quanto as células de produção de última geração, equipadas com tecnologia de ponta." O foco está na redução permanente de custos, na otimização da eficiência e na capacidade de implementar tecnologias modernas de fabricação.
Em 1959, porém, a situação era bem diferente, quando o PC-6 Porter decolou pela primeira vez no aeródromo de Stans. Uma aeronave universal robusta de construção totalmente metálica, também conhecida como "jipe com asas", tão versátil quanto um canivete suíço. Os PC-6 eram montados exclusivamente manualmente. Os funcionários tinham que ser experientes, e as tolerâncias eram maiores do que hoje. O mais recente tipo de aeronave, o PC-24, é composto por inúmeras peças, muitas delas fresadas, com tolerâncias na faixa de Mμ. Hoje, a montagem é muito mais rápida, e isso só é possível com tecnologias de fabricação de última geração.
A partir deste ano, o PC-6 não é mais construído, depois de 500 unidades fabricadas chegou ao fim a sua história de sucesso. O sucessor, o PC-12, foi vendido mais de 1650 vezes em todo o mundo desde 1994, sendo a aeronave turboélice monomotor mais popular no mercado hoje.
Logo no início, as primeiras peças feitas de fibra de carbono foram usadas na fabricação de aeronaves. Os primeiros componentes de PRFV e PRFC para o PC-6 também foram produzidos usando o processo de laminação manual, embora ainda em quantidades gerenciáveis.
Quando se trata de fabricação de aeronaves, quase tudo gira em torno da redução de peso. Como resultado, mais e mais peças estão sendo fabricadas a em fibras de carbono e vidro. A grande vantagem é a alta rigidez e dureza, bem como a resistência ao desgaste. O maior desafio é encontrar o equilíbrio entre peso, estabilidade e custo. "Além disso, há fatores como carga útil e espaço utilizável, que deve ser o maior possível." A Pilatus ainda não fabrica peças de suporte de carga em PRFC, mas o departamento de P&D está trabalha intensamente nisso. No caso do PC-24, os compósitos são usados principalmente no revestimento interno e externo. As carcaças e extremidades das asas do motor também são feitas de fibra de carbono, bem como portões do trem de pouso, dutos de ar, tubulações, tampas ou bordas de fuga das asas.
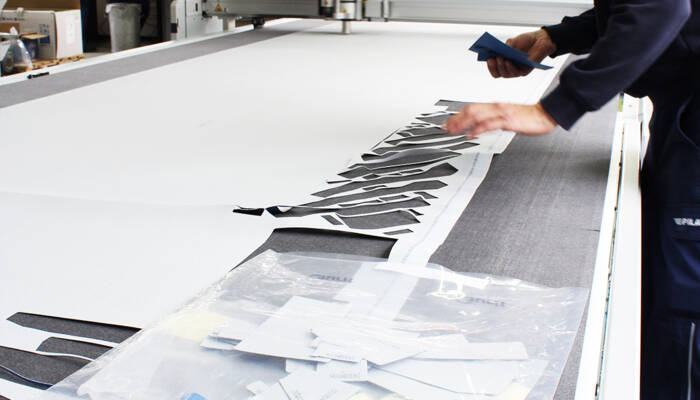
Prepregs, o futuro na fabricação de aeronaves
O ponto de partida para essas peças aeronáuticas são os tecidos de reforço pré-impregnados, os chamados prepregs. Nesse processo, fibras contínuas são umectadas e consolidadas sob pressão e temperatura. Os prepregs têm alta resistência e rigidez, robustos contra desgaste e fadiga, retardantes de chama e insensíveis às influências ambientais.
Os prepregs são entregues em rolos, transportados em caminhão refrigerado e armazenados temporariamente a -19 graus. Para garantir que atinjam a temperatura ambiente no momento do corte, eles são retirados do refrigerador na noite anterior. O material pode permanecer em temperatura ambiente por cinco a 20 dias antes que a resina reaja e endureça. A Pilatus processa cerca de cinco rolos de aproximadamente 90 m2 por dia, cerca de 90 mil m2 por ano. E o consumo não para de crescer. Mais da metade de todos os componentes CFRP e GFRP fabricados pelo departamento de plásticos já estão instalados no novo PC-24. A Pilatus conta com a tecnologia de corte digital da Zünd há mais de 15 anos para o corte de suas folhas de prepreg. A máquina de corte da série PN ainda faz seu trabalho de forma confiável. No entanto, com o aumento da demanda por componentes de fibra de carbono, o limite de capacidade foi atingido. Desde 2019, uma mesa de corte Zünd G3 L-2500 de última geração corta as camadas individuais dos respectivos componentes de forma amplamente automatizada, fazendo a rotulação em linha com um módulo de jato de tinta integrado.
Após o corte, as peças padrão são coletadas em um kit e armazenadas temporariamente no freezer até que estejam prontas para uso. Dependendo dos requisitos de rigidez e resistência, um componente pode consistir em até 350 camadas.
Para peças de padrão e camadas individuais sem dados DXF disponíveis (digitalizador), uma mesa de digitalização, é usada. Os modelos de componentes podem ser então facilmente gravados na mesa e digitalizados. Mesmo pequenas alterações em componentes aprovados pela engenharia podem ser facilmente adaptadas e digitalizadas com a mesa digitalizadora.
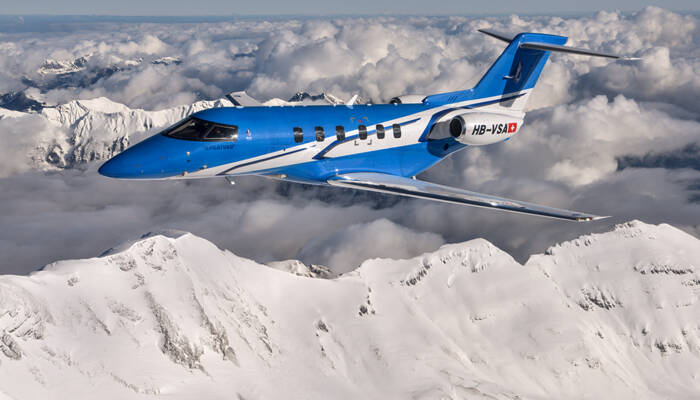
A eficiência do material é um tema constante
A otimização permanente da eficiência também é a chave para o sucesso da Pilatus, conta Patrick Rohrer. "Ao lidar com materiais de alto custo, como fibras de carbono ou de vidro, a eficiência do material e a otimização são um tema contínuo. Estamos constantemente trabalhando para aumentar o grau de utilização e também para reduzir o desperdício. Trata-se de resíduos que ainda são quase impossíveis de reciclar." No entanto, a taxa de resíduos foi reduzida de 30% para 20% atualmente. Nesse ponto, o agrupamento altamente eficiente através do software Zünd Cut Center (ZCC) desempenha um papel importante. Por um lado, as peças padrão são aninhadas estaticamente. Isso significa que um item, ou seja, suas camadas individuais, é aninhado pelo número de pedido. "O aninhamento dinâmico, ou seja, vários trabalhos em um único trabalho de corte, também é usado sempre que relevante." Isso aumenta ainda mais a taxa de utilização da matéria-prima.
O processo como um todo é único
O fato de a Zünd ter conquistado novamente o contrato para a modernização das máquinas do departamento de plásticos deve-se, em parte, a certos pontos em comum entre as duas empresas. A Zünd oferece uma solução global única e modular, comenta Patrick Rohrer. Assim como a Pilatus, a Zünd também está claramente comprometida com a Suíça como local de produção. É no país que a empresa desenvolve e produz soluções de alta tecnologia de ponta para os mercados mundiais, contando com especialistas altamente qualificados. As curtas distâncias que garantem a cooperação bem-sucedida são um fator importante, enfatiza Rohrer para finalizar. "Podemos contar com 15 anos de experiência em tecnologia de corte da Zünd, o que é muito relevante. A Zünd oferece soluções abertas e modulares com contratos de serviço opcionais e software extremamente confiável, sem obsolescência programada. É exatamente isso que significa vantagem real para o cliente." A Zünd dá grande importância ao atendimento de excelência ao cliente, outra semelhança entre as duas empresas.
